Проверка качества выполненного ремонта.
Надеюсь, не стоит объяснять к чему может привести неквалифицированный или некачественно выполненный ремонт двигателя. Контроль над качеством ремонта таких деталей двигателя как блок цилиндров, головка блока цилиндров, коленчатого вала, а также других деталей, ремонт которых производился сторонними организациями (например, мастерскими, специализирующимися на расточке блоков цилиндров) целесообразно проводить непосредственно у исполнителя (т.е. «не отходя от кассы»). Для проверки необходим измерительный инструмент и некоторый навык. Наиболее распространённые ошибки, имеющие место при ремонте блоков цилиндров двигателя следующие:
- Низкое качество зеркала цилиндров.
Является следствием нарушения технологии обработки поверхности цилиндра (хонингования), несоответствия технической оснащённости мастерской современным требованиям, низкой квалификации или халатности исполнителя;
- Отклонение геометрии цилиндра (конусность, овальность, корсетность, бочкообразность) выше допустимых пределов (рис. 6.11).

Конусность и овальность цилиндров после расточки и финишной обработки поверхности не должна превышать 0, 01 мм. При больших значениях не обеспечивается должное прилегание поршневых колец к поверхности цилиндра и как следствие, увеличивается расход масла, уменьшается компрессия в цилиндре и общий ресурс двигателя. Корсетность или бочкообразность цилиндра является следствием низкой квалификации мастера, производящего расточку блока. Корсетность возникает при избыточном выводе хонинговальной головки за верхнюю и нижнюю части цилиндра, бочкообразность, наоборот, из-за её недостаточного вывода. Проверяется путём измерения диаметра цилиндра нутромером. Измерения проводятся по двум, взаимно перпендикулярным, осям в трёх плоскостях (в верхней, средней и нижней частях цилиндра);
- Несоответствие междуосевых расстояний цилиндров.
Расстояние между осями цилиндров (рис. 6.12а) задаётся конструкцией двигателя (например, для двигателей автомобилей ВАЗ это расстояние равно 95, 0 мм.) и независимо от номера выполняемого ремонта, должно оставаться постоянной величиной. Несоответствие межосевых расстояний, как правило, является следствием неправильной установки блока цилиндров на расточку. Проверяется путём измерения расстояния между осями пар цилиндров с помощью штангельциркуля или другого измерительного инструмента;
- Не параллельность осей цилиндров (оси цилиндров не перпендикулярны привалочной плоскости блока цилиндров и оси коленчатого вала) или оси цилиндров не лежат на одной плоскости (рис. 6.12б, в).
Является следствием неверной установки блока цилиндров на расточку;
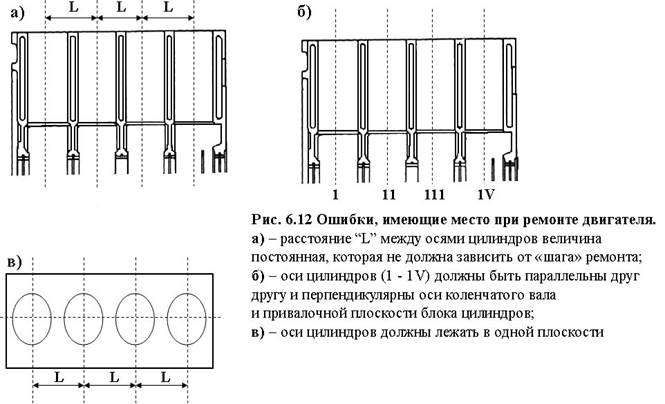
- Несоответствие установочного зазора между цилиндром и поршнем заданной величине.
Является следствием низкой квалификации мастера или его халатности.
Зазор между цилиндром и поршнем регламентируется техническими условиями. В ряде случаев и только осознано, его величина может быть изменена в сторону увеличения. Решение об увеличении установочного зазора принимает мастер, производящий ремонт двигателя. Мастер – станочник производит расточку цилиндров двигателя под заданный ремонтный размер, оставляя припуск на хонингование примерно 0, 05-0, 06 мм. с каждой стороны цилиндра. При хонинговании расточенного цилиндра, мастер учитывает диаметр поршня, который будет установлен в данный цилиндр. Проверка установочного зазора осуществляется путём измерения диаметра цилиндра и диаметра поршня. Величина зазора определяется как разница измеренных диаметров.
- Неплоскостность привалочной плоскости блока цилиндров.
Проверка неплоскостности осуществляется с помощью набора щупов и лекальной (слесарной) линейки, прикладываемой к плоскости. Аналогичным способом контролируется привалочная плоскость головки блока.
Ошибки, возникающие при ремонте коленчатого вала следующие:
- Низкое качество рабочей поверхности шеек (кулачков) вала;
- Эллипсность шатунных и опорных шеек вала;
- Несоответствие размеров шатунных и опорных шеек вала заданным величинам.
6.8. Комплектование деталей.
Комплектование предшествует сборке двигателя и проводится с целью установки в двигатель деталей должного качества и размерности, обеспечения необходимых допусков и посадок. Основой комплектования являются технические условия. Можно выделить несколько способов (методов) комплектования деталей:
- Селективный метод (метод групповой заменяемости).
Данным способом комплектуются поршни, поршневые пальцы, поршневые кольца и некоторые другие детали. Сущность метода заключается в том, что изготовленные запасные части группируются производителем по массе и размерам и соответствующим образом маркируются (цифрой, краской, буквой латинского алфавита, символом и т.п.). При сборке двигателя в него устанавливаются детали, принадлежащие одной размерной группе, чем обеспечивается соблюдение технических условий сборки, регламентированных допусков и посадок.
- Метод полной взаимозаменяемости, т.е. без подгонки деталей друг к другу.
Подобным образом заменяется, например, цепь и звёздочка ГРМ, подшипник качения в своём гнезде и др. детали.
- Метод измерения и подгонки деталей основан на измерении размеров двух или более деталей или зазоров между ними, а так же масс деталей. При несоответствии замеренных величин техническим условиям, детали или заменяются более подходящими, или подгоняются друг к другу. На рисунке рис. 6.13, в качестве примера, показаны регламентированные размеры деталей одного из двигателей.
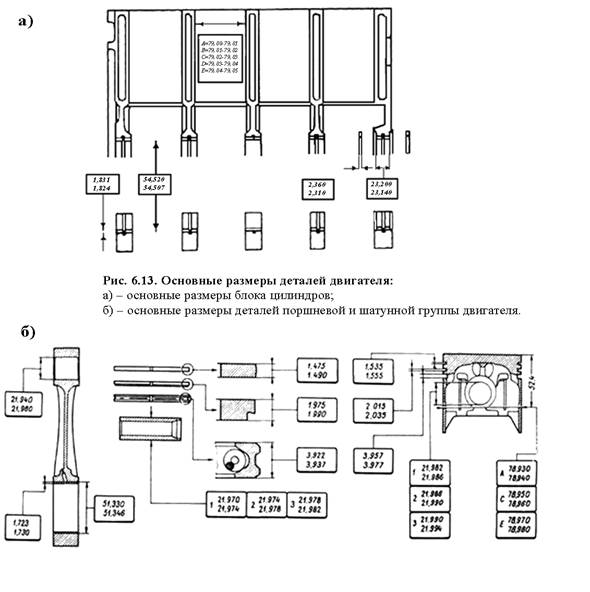
Процессу комплектования деталей предшествует их мойка. Детали, подвергавшиеся ремонту, отмываются от абразивной пыли, смазывающих и охлаждающих жидкостей (СОЖ). Целью мойки является недопущение попадания грязи и абразивного материала в пары трения в процессе сборки двигателя и после ввода двигателя в эксплуатацию. Повышенное внимание следует уделить очистке закрытых каналов и полостей (полостей рубашки охлаждения, масляных каналов и т.п.). Каналы прочищаются ёршиками, промываются под давлением и продуваются сжатым воздухом. Очистка каналов, полостей и отверстий должна проводится при снятых технологических заглушках, и предшествовать мойке самих деталей, так как при мойке из каналов может выходить большое количество загрязняющего материала, оседающего на поверхности деталей. В целом, мойка деталей перед сборкой агрегата производится так же, как это было описано в разделе «Мойка деталей двигателя». Напомним, что в «глухих» резьбовых отверстиях, после мойки, не должно оставаться промывочных и смазывающих жидкостей, а при мойке узлов и агрегатов, имеющих закрытые подшипники качения, следует исключить попадание моющих растворов во внутренние полости подшипников. После мойки и сушки корпусные детали двигателя при необходимости окрашиваются.
6.9. Сборка соединений и двигателя.
Порядок сборки двигателя достаточно подробно описывается в сервисной литературе. При прочтении литературы следует обращать внимание на текст, выделенный курсивом или жирным шрифтом. Как правило, такой текст содержит требования обязательные для исполнения ремонтным персоналом. Технология сборки двигателя определяется его конструкцией и может различаться в зависимости от модели. Тем не менее, имеет место ряд технологических особенностей сборки, общих для большинства существующих конструкций.
При сборке двигателя должны быть обеспечены:
1). Необходимые натяги/зазоры в соединениях и в парах трения. Например, между гильзой и её гнездом, поршнем и гильзой, поршневым пальцем и отверстием поршневого пальца, поршневым пальцем и верхней головкой шатуна (втулкой верхней головки шатуна), кольцами и канавками поршня, краями поршневых колец (в замке кольца), седлом клапана и его посадочным отверстием в головке блока цилиндров и т.п.
Условно, все установочные зазоры можно поделить на тепловые, которые компенсируют тепловое расширение металла при нагревании, и масленые, которые обеспечивают нахождение смазки между трущимися поверхностями. Величины и тех, и других зазоров строго регламентированы техническими условиями. Нарушение рекомендаций приводит к заклиниванию деталей при нагревании, разрушению деталей из-за недостатка смазки и т.п.
Натяг, т.е. соединение без зазора, обеспечивает неподвижность охватываемой детали (втулки) при тепловом расширении охватывающей детали. Натяг обеспечивается установкой детали большего диаметра в отверстие, меньшего диаметра, для чего, либо «нагревают отверстие», либо охлаждают (например, в жидком азоте) втулку.
2). Подборка (комплектование) деталей по массе. Уравновешенность двигателя достигается, в том числе тщательной подборкой деталей по весу. Чтобы избежать нудной процедуры взвешивания и подгонки веса деталей можно рекомендовать приобретать детали в комплекте для одного двигателя. Как правило, добросовестный производитель гарантирует соответствие массы и размерности запасных частей в приобретаемом Вами наборе.
3). Ориентирование деталей. При сборке соединений необходимо соблюсти правильную «ориентацию» поршней и шатунов в цилиндрах двигателя, поршневых колец в канавках поршня, крышек шатунов на разъёме нижней головки шатунов и крышек коленчатого вала на его опорах. Ориентируются и некоторые другие детали двигателя.
4). Усилия, последовательность и порядок затяжки резьбовых соединений. От общего объёма сборочных работ автомобиля сборка резьбовых соединений составляет примерно одну треть. При выполнении сборочных операций и работе с резьбовыми соединениями следует помнить и выполнять некоторые общие правила:
- Весь используемый крепёж должен быть абсолютно чистым, прямым, с ненарушенной резьбой и несмятыми гранями головок. Повреждённый крепёж подлежит обязательной замене.
- Соединения, в которых предусматривается законтривание болтов (гаек), должны быть соответствующим образом зафиксированы. Способом фиксирования болтов и гаек может быть шплинтование или установка под опорную поверхность крепежа гроверных и стопорных шайб. Между стопорной шайбой и мягкой металлической поверхностью (например, алюминиевой) всегда устанавливаются плоские опорные шайбы;
- Следует применять крепёж соответствующей размерности и соответствующего класса прочности.
Класс прочности болтов маркируется на головке болта в виде цифры или радиальной насечки. Класс прочности шестигранных гаек обозначается либо цифрой, либо насечкой в виде точек (рис. 6.14). Чем больше количество насечек, или чем выше номер цифрового кода, тем выше прочность и допустимое усилие закручивания гайки (болта). Имеет место следующий ряд маркировочных чисел: 3.6; 4.6; 4.8; 5.6; 5.8; 6.8; 8.8; 10.9; 12.9. Крепёж ниже 5-го класса прочности, как правило, не маркируется.
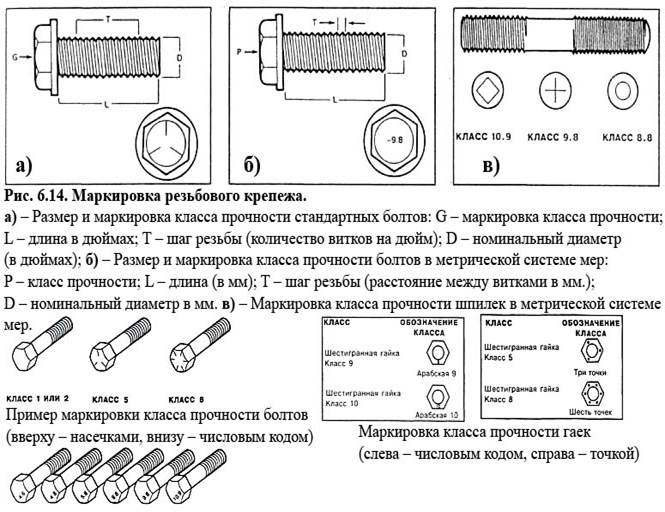
- В глухих резьбовых отверстиях не должно оставаться эксплутационных и иных жидкостей. Так как жидкость не сжимается, то при вкручивании болта в отверстие возможно образование трещин в детали;
- При необходимости обеспечения герметичности резьбы, на резьбу наносят специальный герметик;
- Резьбовое соединение затягивается так, чтобы была обеспечена надёжность соединения. Крепёж должен обеспечивать соединение деталей с усилием, достаточным для предотвращения их смещения под воздействием рабочих нагрузок. В случае чрезмерных усилий затяжки возможен не только срыв резьбы, но и деформация самих соединяемых деталей и отверстий (например, цилиндров). Предусмотренный момент затяжки резьбового соединения приводится в технических условиях и, как правило, выражается в кгс х м. (килограмм-сила умноженная на метр) либо в Н х м (ньютон умноженный на метр). Усилия затяжки, регламентируемые ТУ, обязательны для выполнения ремонтным персоналом. Контроль затяжки резьбовых соединений осуществляется динамометрическим ключом.
Для резьбового крепежа ниже 5-го класса прочности, при отсутствии ТУ, максимальные усилия затяжки можно вычислить по формуле: Mmax=O - 4 (кгс х м); где Mmax – максимальное усилие затяжки, O -диаметр резьбы крепежа. Пример: Гайка с диаметром резьбы 8мм, будет иметь максимальное усилие затяжки Mmax=8 - 4=4 (кгс х м). - Порядок затяжки определяется тем, за сколько «подходов» достигается регламентируемое (номинальное) усилие затяжки крепёжной детали. Порядок затяжки, как и усилие, определяется ТУ. При отсутствии рекомендаций изготовителя можно придерживаться общего правила:
1) Если усилие затяжки не превышает 14 кгс/м, затяжка осуществляется за четыре «подхода»
- Подводка болта (гайки) к плоскости детали;
- Подтяжка болта (гайки) усилием в половину номинального момента;
- Затяжка болта (гайки) номинальным моментом;
- Проверка правильности затяжки всего крепежа.
2) Если усилие затяжки больше 14 кгс/м, затяжка осуществляется за пять «подходов»
- Подводка болта (гайки) к плоскости детали;
- Подтяжка болта (гайки) усилием в одну треть от номинального момента;
- Подтяжка болта (гайки) усилием в две трети от номинального момента;
- Затяжка болта (гайки) номинальным моментом;
- Проверка правильности затяжки всего крепежа.
- Последовательность затяжки (схема затяжки) должна соответствовать схеме, предложенной изготовителем. Схемы затяжки головок блоков некоторых двигателей и других соединений представлены на рис. 6.15.
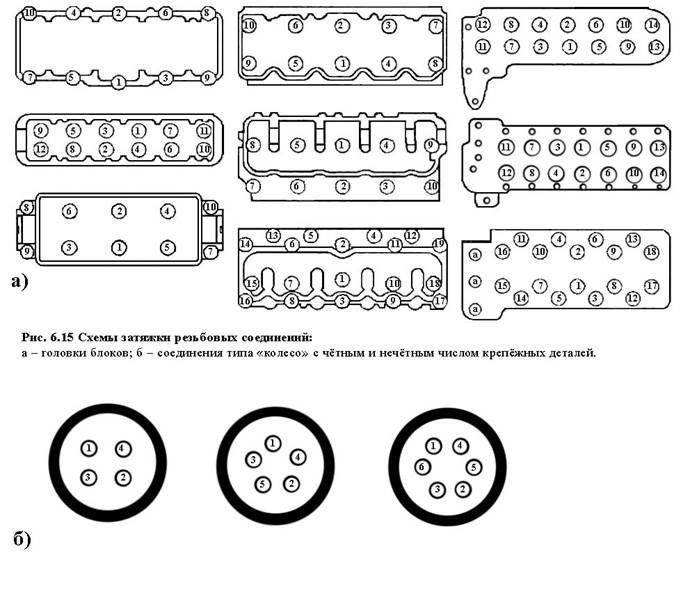
Требование соблюдать последовательность затяжки резьбового крепежа определяется необходимостью равномерно распределить прикладываемые нагрузки по плоскости детали, обеспечить должную прочность и герметичность соединения. Общие рекомендации к схеме затяжки следующие:
- «Длинные детали» (например, такие как головка блока или корпус подшипников распределительного вала) затягиваются от центра к краям «по спирали» или «по окружности».
- Соединений типа «колесо» с четырьмя, пятью, шестью и более соединениями затягиваются «крест на крест» (снежинкой), при чётном числе крепёжных деталей или «через один», при нечётном числе крепёжных деталей (рис. 6.15).
6.9.1. Установка гильз цилиндров в блок двигателя.
Мокрые гильзы устанавливаются в гнёзда блока цилиндров с зазором. От осевого перемещения, гильзы удерживаются головкой блока. Для надёжного прижатия гильзы, её верхняя часть должна выступать над привалочной плоскостью блока цилиндров на рекомендованную величину (0, 02 – 0, 12 мм.). Величина выступания гильзы, как правило, регулируется подбором шайб, устанавливаемых под опорный бурт. Эти же шайбы уплотняют гильзу в гнезде, предотвращая попадание охлаждающей жидкости из рубашки охлаждения через стык гильзы с её опорой в картер двигателя. В конструкциях двигателей, где применение шайб не предусмотрено, на привалочную плоскость бурта гильзы или посадочную плоскость гнезда, наносится тонкий слой специального термостойкого клея или герметика. Проверка выступания гильзы показана на рис. 6.16.
Сухие гильзы удерживаются в гнёздах блока цилиндров натягом. В зависимости от требуемой величины натяга, для соединения чугунной гильзы и алюминиевого блока цилиндров, необходимо обеспечить разницу температуры соединяемых деталей в пределах 100 - 180 градусов С, для чего блок цилиндров нагревают в муфельной печи или, помещая его в горячую воду, а гильзу охлаждают «сухим льдом» или жидким азотом. В «сухом льду» (твёрдой углекислоте) возможно охлаждение до -80 градусов С (реально, до -60 градусов), а в жидком азоте до -140 градусов. Нагревание блока цилиндров открытым пламенем равно как и запрессовка чугунных гильз в алюминиевый блок давлением, недопустимо.
Гильзование чугунных блоков цилиндров, в ряде случаев, разрешается проводить способом запрессовки.
Запрессовка чугунных гильз в чугунный же блок цилиндров, как правило, возможна при величине натяга, не превышающем 0, 05 мм. (редко более). Запрессовку гильз осуществляют с помощью пресса. При отсутствии заводского пресса, приспособление для запрессовки можно сконструировать из металлических швеллеров, соединив их с помощью сварки в виде рамы должного размера, и гидравлического или винтового домкрата. В продаже можно так же увидеть, более компактные и простые в применении, винтовые приспособления. Производить запрессовку детали в отверстие ударом запрещается. Для упрощения процесса запрессовки, можно нагреть блок или охладить гильзу, обеспечив разницу температур соединяемых деталей, примерно в 60 - 100 градусов С. При указанной величине натяга и разнице температур, гильза должна опустится в гнездо без применения каких либо приспособлений. При необходимости «помочь» гильзе опустится в гнездо можно постукивая по ней деревянной киянкой или молотком через деревянную проставку.
6.9.2. Установка коленчатого вала в опоры двигателя.
Отремонтированный коленчатый вал устанавливается в подшипники (вкладыши) соответствующего ремонтного размера. Ремонтный размер вкладыша выбивается в виде цифры на его тыльной (нерабочей) поверхности и должен соответствовать размерности произведённого ремонта коленчатого вала. При отсутствии рабочей маркировки вкладыша его размер вычисляется путём измерения его толщины микрометром. Новый/неизношенный вкладыш должен вставляться в постель с небольшим натягом и не должен выпадать из постели при переворачивании блока цилиндров. Отверстия для смазки во вкладышах должны совпадать с отверстиями в постелях. Верхние и нижние вкладыши коленчатого вала (вкладыши опоры и вкладыши крышки) могут быть не взаимозаменяемые. Вкладыши средней опоры КВ могут иметь большую ширину (площадь). Перед установкой коленчатого вала поверхности вкладышей и шеек коленчатого вала обильно смазываются. После установки в постели блока коленчатый вал закрепляется крышками. Крышки коленчатого вала равномерно затягиваются болтами. Усилия затяжки должны соответствовать ТУ и контролируются динамометрическим ключом. Вал, смазанный и установленный в картер блока должен легко (от руки) вращаться в опорах. Свободное вращение вала является условием правильности сборки. При наличии заедания вала необходимо разобрать соединение, найти и устранить причины заедания.
Причины тугого вращения коленчатого вала могут быть следующими: 1) несоответствие крышек и вкладышей местам их установки; 2) неправильное положение крышек на опорах; 3) несоответствия размера вкладышей произведённому ремонту; 4) несоответствие диаметра коренных шеек произведённому ремонту; 5) несоответствие толщины упорных полуколец; 6) несоответствие усилия затяжек крепежа крышек; и др.
В опоре где имеет место заедание масло, нанесённое на поверхность деталей перед сборкой, после нескольких оборотов вала мутнеет (т.к. содержит мельчайшие частицы антифрикционного состава вкладышей), а рабочая поверхность вкладыша имеет блестящий след от контакта с шейкой вала (т.н. затир).
Осевое перемещение вала контролируется с помощью индикатора часового типа (рис. 6.17) или от руки (при «качании» коленчатого вала осевой зазор вала не должен ощущаться «на ощупь»). Величина зазора регулируется подбором упорных полуколец (колец) соответствующей толщины. Если величина зазора, измеренного индикатором, больше максимально допустимого (0, 25-0, 35 мм), упорные кольца заменяются новыми или кольцами ремонтных размеров.
Подытожим сказанное:
- Перед установкой в двигатель шейки коленчатого вала и их опоры обильно смазываются моторным или трансмиссионным маслом;
- Вкладыши вала должны входить в постели с небольшим натягом, отверстия для смазывания во вкладышах должны совпадать с отверстиями в опорах/крышках, вкладыш средней опоры КВ может иметь большую ширину, вкладыши опоры и вкладыши крышки могут быть не взаимозаменяемыми;
- Крышки КВ не взаимозаменяемые и устанавливаются строго на свои постели, замки вкладышей всех крышек должны «смотреть» в одну сторону, для правильной установки крышек их маркируют соответствующим образом (как правило, цифрой по номеру опоры или зарубками);
- Крепление крышек КВ является ответственным соединением и контролируется динамометрическим ключом.
6.9.3. Сборка шатунов с поршнями.
Перед сборкой необходимо подогнать поршни и шатуны двигателя по массе к самому лёгкому поршню (шатуну). Разница масс (
) поршней и шатунов для одного двигателя не должна отличаться более чем на 1 – 1, 5% от среднеарифметического (
)массы всех поршней (шатунов) двигателя.
, где
- сумма масс всех поршней (шатунов) двигателя;
- число поршней (шатунов) двигателя.
Если разница масс поршней превышает указанную величину «лишний» металл, в пределах разумной достаточности, «бархатным» напильником снимается с нижней наружной стороны бобышек или в ином, указанном производителем месте поршня (рис. 6.18.).
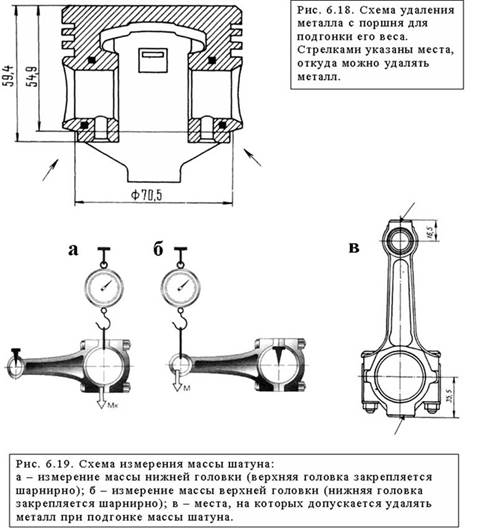
При подгонке массы шатунов металл стачивается с бобышек верхней и/или нижней головки шатуна. Так как верхняя головка шатуна при работе двигателя совершает поступательные движения, а нижняя – вращательные, головки шатуна правильно взвешивать по отдельности. При взвешивании верхней головки шатуна, нижняя головка закрепляется на шарнирной опоре (например, на шейке коленчатого вала). При взвешивании нижней головки, на шарнирной опоре закрепляется верхняя головка (например, на поршневом пальце, зажатом в тисках). Надеюсь, рисунок рис. 6.19, пояснит сказанное выше.
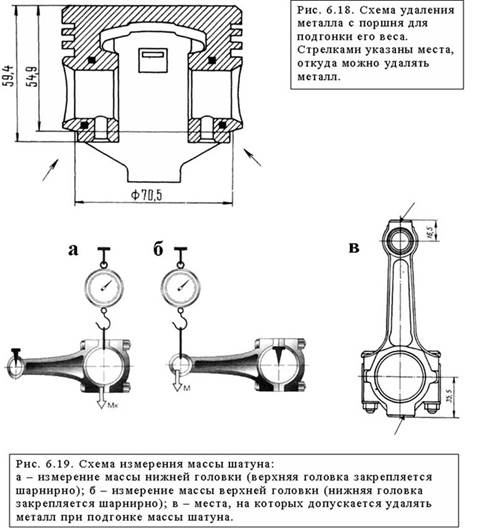
Сумма масс «верхней» и «нижней» частей шатуна должна быть равна массе всего шатуна. При несоответствии масс верхних головок шатунов, металл стачивается с их верхних бобышек, при несоответствии масс нижних головок - нижних. При спиливании «лишнего» металла с бобышек головок шатуна расстояние от центра отверстия головки до плоскости бобышки не должно стать меньше допустимого (регламентируется изготовителем). При принятии решения о подгонке масс шатунов следует иметь ввиду, что уменьшение массы нижней головки оправдано лишь для двигателей, имеющих полностью сбалансированные коленчатые валы симметричные относительно средней коренной шейки (рядные четырёхцилиндровые, рядные шестицилиндровые и V - образные двенадцатицилиндровые двигатели). Для других двигателей слишком лёгкие или тяжёлые шатуны лучше заменить более подходящими по весу.
Если на двигатель устанавливаются новые шатуны их стоит промаркировать любым доступным способом (например, клеймом или кернером) по месту установки (т.е. по цилиндрам двигателя). Номер соответствующего цилиндра выбивается на нижней головке шатуна и на его крышке. Нанесённые метки (номера) должны быть обращены в одну сторону. Если устанавливаются «старые» шатуны, они должны быть поставлены в «свои» цилиндры в соответствии с имеющимися метками.
На самом деле, если заменялись поршни, то нет никакой разницы, в какой цилиндр устанавливается тот или другой шатун. Но следует понимать, что при последующих ремонтах, имеющееся несоответствие между метками номеров цилиндров на шатунах и местом установки шатунов, может внести существенную путаницу и стать причиной возможных ошибок.
Установочные зазоры между поршнем и стенкой соответствующего цилиндра должны соответствовать ТУ. Как уже отмечалось выше, ось отверстия под поршневой палец на большинстве поршней современных двигателей, смещена в сторону действия «большей боковой силы» на 0, 5 – 2, 5 мм. Вследствие этого поршень должен быть установлен в цилиндре строго определённым образом, т.е. сориентирован. Для правильной установки поршня в цилиндр производители деталей помечают «фронтальную» или «тыловую» (реже) часть поршня специальной меткой, выбиваемой на днище поршня или ином месте. Метка может иметь вид стрелки ( > ), или быть в виде буквы « П » (перед), или « F » (фронт), или в виде слова « ПЕРЕД », или слова « НАЗАД ». С конца 70-х, начала 80-х годов фронтальная часть поршней обозначается преимущественно стрелкой. На днище поршня наносится и иная информация о детали (рис. 3.5).
Ориентация шатунов регламентируется производителем в случае ассиметричной конструкции шатуна или наличием у него отверстия для смазывания стенки цилиндра. Отверстие для подачи масла должно быть «нацелено» на наиболее нагруженную стенку цилиндра. При «правом» вращении коленчатого вала (т.е. по часовой стрелке, если смотреть со стороны шкива КВ), наиболее нагруженная стенка цилиндра будет левая. «Правое» вращение коленчатого вала имеют подавляющее большинство двигателей.
Сборка поршня с верхней головкой шатуна происходит через поршневой палец. Палец «плавающего» типа должен входить в отверстие головки шатуна без заедания и не иметь ощутимого радиального люфта во избежание шумной работы двигателя после прогрева. В бобышки поршня «плавающий» палец, как правило, запрессовывается с небольшим натягом, для чего поршень подогревают техническим феном или разогревают в горячей воде до температуры 60-80? С. От осевого перемещения палец «плавающего типа» в бобышках поршня удерживается стопорными кольцами. При установке стопорных колец замок кольца ориентируется по оси поршня (вверх или вниз). Следует проследить, зафиксировалось ли кольцо в канавке бобышки поршня. Стопорное кольцо должно «распрямиться» в канавке и не иметь в нём ощутимого люфта. При несоблюдении этих условий сборки кольцо может «выскочить» из канавки при работе двигателя.
Поршневой палец второго типа (запрессованный в верхнюю головку шатуна), в бобышки поршня должен входить под небольшим усилием руки (рис. 6.20), а в головку шатуна с натягом, регламентируемым ТУ (как правило, не меньше 0, 010 мм.).
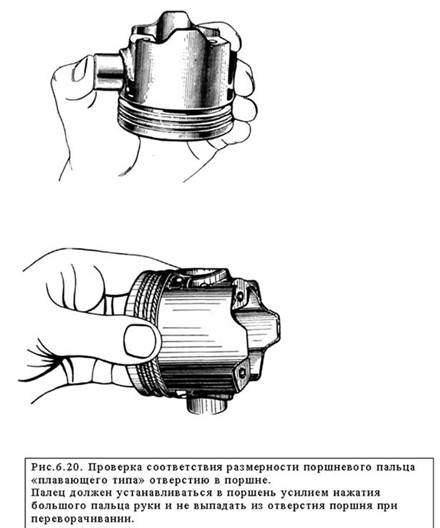
Для посадки пальца в головку шатуна с натягом, шатун разогревают в муфельной (электрической) печи до 240-270? С. Для запрессовки используется специальная оправка (рис. 6.21).
На практике часто используют способ нагревания верхней головки шатуна паяльной лампой. Данный способ прост в применении, но не позволяет контролировать температуру нагрева. Повышение температуры нагрева выше 300? С может привести к изменению структуры металла шатуна и потери натяга, установленного в головку поршневого пальца. Осевое перемещение пальца в головке шатуна на работающем двигателе, в свою очередь, чревато задиром зеркала цилиндра двигателя.
Подытожим. При сборке поршней и шатунов и установке их в двигатель следует придерживаться ряда общих правил:
- Поршни и шатуны для одного двигателя подбираются по массе;
- Поршни и шатуны ориентируются в двигателе определённом образом. Для правильной установки этих деталей в двигателе, на детали наносятся специальные метки;
- Замок стопорного кольца поршневого пальца «плавающего типа» должен быть сориентирован по оси поршня, зафиксирован в канавке бобышки поршня, и не иметь в ней существенных перемещений;
- Пальцы «плавающего типа» устанавливаются в головку шатуна через вкладыш с зазором, а в бобышки поршня с небольшим натягом;
- Пальцы «запрессованные» в верхнюю головку шатуна устанавливаются в неё со значительным натягом, а в бобышки поршня должны входить от небольшого усилия ладони.
6.9.4. Установка поршневых колец на поршни.
Перед установкой колец на поршни (уже собранные с шатунами) следует проверить соответствие зазора в замке кольца с зазором, регламентируемым заводом изготовителем. Зазор обеспечивает тепловое удлинение кольца при прогреве. Слишком малый установочный зазор на работающем двигателе может уменьшиться до нуля и привести к поломке кольца. Поломанное кольцо становится причиной низкой компрессии в цилиндре двигателя, повышенного расхода масла на угар, повышенного расхода топлива и т.п. Поломанное кольцо, заклинившее в канавке поршня, может повредить стенку цилиндра. Величина установочных зазоров в замках компрессионных и маслосъёмных колец разных типов двигателей лежит в пределах 0, 15 -0, 50 мм (иногда более). Для измерения зазора, кольцо опускается в цилиндр двигателя на глубину около 1 см. или устанавливается на специальное приспособление, имитирующее цилиндр. Зазор измеряется плоским щупом (рис. 6.22)..
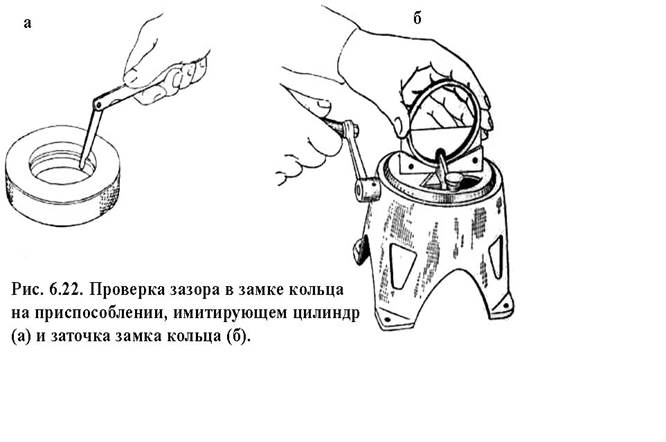
При величине зазора меньше регламентируемого, замок подпиливается на специальном приспособлении или вручную надфилем. Во втором случае, кольцо зажимается в тисках между двумя деревянными брусочками или удерживается руками. При подпиливании замка кольца необходимо обеспечить параллельность его краёв.
Не менее важно обеспечить необходимые зазоры между поверхностями колец и поверхностями поршневых канавок. Зазор измеряется плоским щупом (рис. 6.23) или определяется как разница между шириной канавки, измеренной плиткой (специальный измерительный инструмент), и высотой кольца, измеренного микрометром. Величина этого зазора между неизношенными канавками и их кольцами составляет в среднем 0, 04-0, 06 мм.
Малый зазор может вызвать подклинивание колец на непрогретом двигателе или их «пригоранию» в канавке с потерей подвижности. Малый зазор устраняется притиркой колец абразивным порошком на плоской металлической плите или на листе наждачной бумаги, уложенной на ровную поверхность.
При больших зазорах компрессия в цилиндрах падает, расход масла увеличивается, ухудшается отвод тепла от поршня в стенки цилиндра, кольца перекашиваются в канавках, «закручиваются» и быстро изнашиваются.
Поршневые кольца часто имеют сложную форму рабочей поверхности (поверхности, которая контактирует со стенкой цилиндра). От правильной установки колец на поршень и ориентировки замков колец, зависит нормальная работа двигателя. Так, при неверной установке маслосъёмного кольца (скребком вверх), расход масла в цилиндре увеличивается на 50%. Для правильной установки колец на двигатель, производитель помечает верх кольца специальной меткой (засечкой, надписью « ТОР », « ВЕРХ » или иным образом). При наличии специальных меток, кольца ориентируются меткой в сторону камеры сгорания. Перепутать кольца местами при их установке в канавки поршня, достаточно проблематично, так как и кольца и канавки поршней имеют различную высоту. Расположение колец в канавках поршней разных двигателей показано на рис. 6.24.
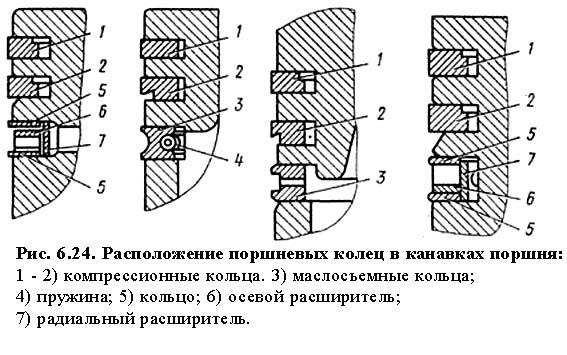
На поршни кольца устанавливаются вручную или с помощью специальных приспособлений (рис. 6.25).
Замки поршневых колец, установленных на поршни, ориентируются одним из двух способов (рис. 6.26):
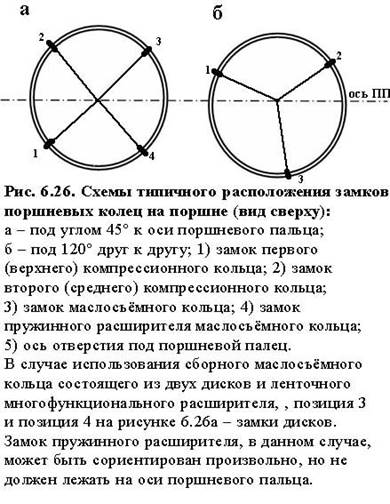
- Под углом 45 градусов к оси отверстия поршневого пальца;
- Под углом 120 градусов друг к другу.
«Ориентирование» замков колец обусловлено необходимостью, обеспечить должное уплотнение поршня в цилиндре и равномерный износ во времени самих колец.
Итак, подытожим. При установке колец на поршень необходимо выполнить некоторые требования:
- Обеспечить необходимый зазор в замке колец;
- Обеспечить необходимый зазор между кольцами и их канавками;
- Обеспечить правильную установку колец на поршень в соответствии с метками, нанесёнными на «верхнюю» часть кольца;
- Обеспечить ориентацию замков колец в пространстве способом, регламентируемым ТУ.
6.9.5. Установка поршней в цилиндры двигателя.
Поршни в сборе с шатунами устанавливаются в цилиндры двигателя с помощью специальной оправки, позволяющей сжать поршневые кольца (рис. 6.27).
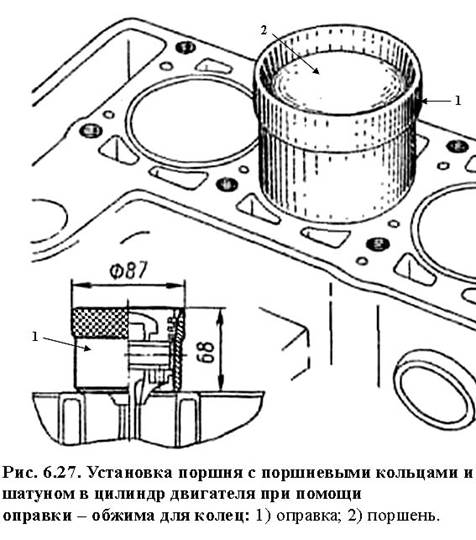
С помощью такой оправки поршень должен легко, небольшим усилием руки входить в смазанный маслом цилиндр. При отсутствии оправки её можно изготовить из тонкой жести, согнув жесть по диаметру поршня. Кольца, при установке поршней в цилиндр, можно сжать и при помощи трёх отвёрток, расположив их под углом 120 градусов друг к другу. Работать, придётся вдвоём, так как для обжатия колец с помощью отвёрток потребуется «три руки», «четвёртая рука» подаёт поршень в цилиндр. Однако этот и некоторые другие способы более трудоёмкие, чем предложенный ранее.
Перед установкой поршней с кольцами и шатунами в цилиндр стоит ещё раз проконтролировать ориентацию этих деталей в двигателе.