Глава 2. АВТОМОБИЛЬНЫЕ ДВИГАТЕЛИ.
Кузов
Кузовы легковых автомобилей, по большей части имеют несущую конструкцию, которая предполагает крепление основных узлов и агрегатов непосредственно к его корпусу. Немногим реже встречаются легковые автомобили, имеющие кузов с несущим основанием или подрамником, ещё реже - рамную конструкцию. Несущий кузов получил распространение с 50-х годов прошлого столетия.
Корпус несущего кузова рис. 1.2 объемный, из листового металла толщиной 0, 5 –2, 0 мм, представляет собой жесткую сварную конструкцию, состоящую из отдельных, предварительно собранных узлов: 1)основания (пола) с передней и задней частями корпуса; 2) левой и правой боковин со стойками дверей и задними крыльями; 3) крыши и 4) передних крыльев. Жёсткость кузова обеспечивается наличием в его составе большого числа профильных элементов из штампованных деталей, которые при соединении создают закрытые коробчатые сечения.
Тип кузова определяется числом функциональных отсеков (объёмов) и конструктивным исполнением. Изготовителями выпускаются автомобили с трёх, двух, и однообъёмными кузовами.
Трёхобъёмный кузов имеет в своём составе моторный отсек, салон и багажное отделение (например, лимузин, купе, седан, кабриолет, хардтоп).
Двухобъёмный кузов имеет моторный отсек и салон, совмещённый с багажным отделением, расположенным в задней части салона (например, универсал, комби, фастбек, хэтчбек).
В однообъёмном кузове моторный отсек, салон и багажник объединены в одно целое (например, минивэны с центральным расположением силового агрегата, пассажирские фургоны типа «буханка»).
Кузов может быть открытым или закрытым. Открытый тип кузова имеет съёмную крышу или складывающийся верх, выполненный из матерчатого или пластикового тента (например, кабриолет, родстер, фаэтон, ландо).
Грузовые типы кузовов легковых автомобилей также могут быть открытыми – «пикап», или закрытыми – «фургон». Грузовая часть кузова таких автомобилей отделена от водителя и пассажиров стационарной перегородкой.
Некоторые типы кузовов легковых автомобилей представлены на рис. 1.3
Шасси
Шасси автомобиля обеспечивает передачу усилия от двигателя к ведущим колёсам, управление автомобилем и его передвижение. В состав шасси входит: 1) силовая передача (трансмиссия); 2) ходовая часть и 3) механизмы управления.
Трансмиссия
Трансмиссия осуществляет передачу крутящего момента от коленчатого вала двигателя к ведущим колёсам, трансформируя его (крутящий момент) в зависимости от условий движения автомобиля. Силовые передачи автомобилей могут иметь существенные отличия.
По степени приспособленности к различным дорожным условиям и назначению, силовые передачи можно разделить на: 1) трансмиссию автомобилей классической компоновки; 2) трансмиссию автомобилей с приводом на передние колёса; 3) трансмиссию автомобилей повышенной проходимости с «колёсной формулой – 4х4»; 4) трансмиссию автомобилей дорожной проходимости с «колёсной формулой – 4х4».
Расположение узлов и агрегатов трансмиссии автомобилей различного назначения показаны на рис. 1.4.
Автомобиль классической компоновки имеет привод на задние колёса и переднее продольное размещение силового агрегата. Трансмиссия такого автомобиля состоит из: 1) сцепления, 2) коробки передач, 3) карданной передачи и 4) ведущего моста, в котором размещается главная передача с дифференциалом и полуосями.
Сцепление обеспечивает соединение двигателя и трансмиссии при движении автомобиля, а также осуществляет передачу вращения от коленчатого вала на валы коробки передач. Когда при изменении условий движения необходимо переключить передачу сцепление отсоединяет вал двигателя от трансмиссии. Сцепление легковых автомобилей, имеющих механическую трансмиссию - фрикционное, сухое с одним ведомым диском и механическим или гидравлическим приводом.
Однодисковое фрикционное сцепление имеет 1) ведомый диск со ступицей, гасителем крутильных колебаний ( демпфером ) и фрикционными накладками; 2) нажимной диск; 3) диафрагменную нажимную пружину; 4) кожух сцепления и некоторые другие детали.
Общее устройство сцепления легкового автомобиля показано на рис. 1.5
В автомобилях с автоматическими трансмиссиями используются гидродинамические трансформаторы и коробки передач, действующие автоматически, в зависимости от скоростного и нагрузочного режима движения автомобиля.
Коробка передач служит для изменения тягового усилия на колёсах, а также для получения заднего хода и отсоединения ведущих колёс от двигателя. На легковых автомобилях, как правило, применяются двух или трёхвальные коробки передач.
В трансмиссиях с ручным или полуавтоматическим переключением передач применяются механические коробки в основном с цилиндрическими шестернями внешнего зацепления.
В автомобилях с автоматическими трансмиссиями применяются как вальные, так и планетарные коробки передач, управление переключением передач в которых осуществляется автоматически многодисковыми сцеплениями, работающими в масляной ванне, и ленточными тормозами, позволяющими переключать передачи без разрыва потока мощности (т.е. без переключения на «нейтральную» передачу). Количество многодисковых сцеплений и ленточных тормозов зависит от числа передач в коробке.
Трансформация передаваемого от двигателя крутящего момента посредством переключения передач в коробке передач достигается введением в зацепление шестерён различного диаметра, меняющих как соотношение между числами оборотов коленчатого вала двигателя и ведущих колёс автомобиля, так и величину тяговых усилий.
Величина изменений указанных характеристик определяется передаточным числом передачи (чем больше передаточное число передачи, тем сильнее изменяется крутящий момент). Передаточное число в общем случае равно отношению числа зубьев (диаметра) ведомой шестерни к числу зубьев (диаметру) ведущей.
Механическая коробка передач имеет корпус, в котором размещаются: 1) первичный, вторичный и промежуточный валы; 2) шестерни передач; 3) синхронизаторы; 4) штоки и вилки переключающего механизма; 5) рычаг переключения передач и другие детали. Общее устройство пятиступенчатой коробки передач показано на рис. 1.6.
Карданная передача осуществляет передачу усилия от коробки передач на главную передачу ведущего моста автомобиля. Вследствие того, что при движении автомобиля его ведущий мост совершает колебания в вертикальной и горизонтальной плоскостях, карданная передача должна передавать крутящие моменты при постоянно изменяющихся углах наклона между валами и расстояниях между передней и задней осями.
Карданная передача состоит из: 1) карданного вала (валов); 2) карданных шарниров или шарниров равных угловых скоростей; 3) промежуточных опор и эластичных муфт карданного вала (валов). Устройство карданной передачи полноприводного автомобиля показано на рис. 1.7.
Главная передача обеспечивает передачу крутящего момента с карданного вала на полуоси под углом 90° и изменяет крутящий момент в соответствии со своим передаточным числом. Главные передачи легковых автомобилей по большей части одинарные и состоят из двух шестерён – ведущей и ведомой. Ведущая шестерня приводится в движение от карданного вала. Ведомая шестерня крепится к корпусу дифференциала и передаёт вращение на полуоси.
Дифференциал служит для распределения крутящего момента между ведущими колёсами и позволяет им вращаться с разной скоростью при движении автомобиля в повороте или по неровной дороге. Наибольшее распространение имеют дифференциалы с коническими шестернями. Дифференциал состоит из корпуса (коробки) дифференциала, в котором размещаются: 1) полуосевые шестерни; 2) саттелитовые шестерни и 3) ось саттелитов.
Полуоси передают крутящий момент от дифференциала на ведущие колёса автомобиля.
Главная передача с дифференциалом и полуосями устанавливается в балке ведущего моста. Балка моста имеет центральную часть – картер и полуосевые рукава. Балка является задней осью автомобиля и крепится к кузову через элементы подвески. Балки бывают разъёмные и неразъёмные. Устройство ведущего моста с главной передачей и дифференциалом показано на рис. 1.8
Трансмиссия автомобилей с приводом на передние колёса отличается от рассмотренной выше тем, что не имеет заднего ведущего моста и карданной передачи. Главная передача и дифференциал размещаются в дополнительном картере коробки передач, а передача усилий от дифференциала на колёса осуществляется через валы привода передних колёс с шарнирами равных угловых скоростей (ШРУС).
Трансмиссия автомобилей повышенной проходимости «внедорожников» с «колёсной формулой – 4х4» дополнительно имеет вторую коробку передач – раздаточную коробку; несколько карданных передач; два ведущих моста – передний и задний, с главными передачами и межколёсными дифференциалами. Раздаточная коробка, как правило, снабжена понижающей передачей и может иметь межосевой дифференциал (для версий с постоянным (т.е. не отключаемым) приводом на все колёса). Также предусматривается механизм блокировки одного или нескольких дифференциалов. На части техники применяются самоблокирующиеся дифференциалы или дифференциалы повышенного трения, а также механизмы отбора мощности на привод вспомогательных механизмов, например лебёдки.
К внедорожникам предъявляются повышенные требования, касающиеся силы тяги, прочности подвески, кузова, а также других узлов и систем. К компоновочным особенностям таких машин, можно отнести короткую базу и высокий клиренс (дорожный просвет) которые, наряду с вышеперечисленными характеристиками, позволяют преодолевать различную степень бездорожья.
Трансмиссия автомобилей дорожной проходимости с «колёсной формулой – 4х4» предназначена для эксплуатации на дорогах с твёрдым покрытием, но может иметь «компромиссную» конструкцию, т.е. одновременно отвечать требованиям как «внедорожника», так и «обычного» автомобиля с приводом на передние или задние колёса. Чаще всего применяется схема, где передние колёса являются основными ведущими, а задний мост подключается автоматически и по мере необходимости. В качестве механизма автоматического подключения заднего моста используются многодисковые вязкостные муфты или механизмы повышенного трения, размещаемые в раздаточной коробке. Сама раздаточная коробка, как правило, монтируется в одном корпусе с коробкой передач.
Трансмиссия современных автомобилей может иметь электронные или электронно-гидравлические устройства управления силой тяги ведущих колёс, к которым относят противобуксовочную систему (ASR). Противобуксовочная система предотвращает проворачивание колёс относительно дорожного покрытия, при излишнем крутящем моменте тем самым, обеспечивая плавное трогание автомобиля с места, оптимальную тягу на колёсах и поддержание курсовой устойчивости автомобиля.
Ходовая часть
Ходовая часть автомобиля состоит из: 1) несущего основания; 2) передней и задней осей; 3) подвески и 4) колёс.
Несущим основанием легкового автомобиля является несущий кузов или рама. Так же, несущее основание может быть образовано элементами рамы, соединёнными с профильными элементами панели пола. Полученная таким образом конструкция, представляет собой отдельный узел автомобиля. К несущему основанию (кузову или раме) крепятся все части и механизмы автомобиля. На раму устанавливается и сам кузов (кабина).
Передние и задние оси автомобиля могут быть ведущими и неведущими. Ведущими осями являются балки ведущих мостов (переднего и/или заднего). Неведущая ось грузового автомобиля представляет собой стальную балку при помощи рессор соединяемую с рамой. У легковых автомобилей, имеющих независимую подвеску колёс, понятие неведущей передней и задней оси отсутствует. В передней части несущего кузова автомобиля с задней ведущей осью имеется стальная балка – поперечина, прикрепляемая к кузову жёстко. В задней части несущего кузова автомобиля с приводом на передние колёса также имеется поперечная балка, называемая соединителем рычагов, которая присоединяется к кузову через элементы подвески. К балкам крепятся рычаги подвески и другие детали.
Подвеска гасит колебания кузова, возникающие при движении автомобиля, смягчает и поглощает удары колёс о неровности дороги тем самым, обеспечивая больший комфорт водителю и пассажирам, сохранность грузов и эксплутационную безопасность автомобиля. Подвеска автомобилей бывает зависимой и независимой. Следует различать рессорные, рычажные, пружинные, торсионные, гидропневматические и пневматические подвески, а также подвески смешанного типа. Основные типы подвесок показаны на рис.1.9а и рис.1.9 б


Колёса автомобиля могут быть ведущими, ведомыми и управляемыми. Ведущими колёсами могут являться передние колёса, задние колёса или все колёса автомобиля. Если ведущей является одна пара колёс (независимо – передняя или задняя), то автомобиль имеет колёсную формулу 4х2; если ведущими являются все четыре колеса, то – 4х4.
Управляемые колёса у легкового автомобиля – передние.
Управляемые передние колёса устанавливаются на ось с углом развала в вертикальной плоскости, равным 0 - 3° и схождением 2 – 4 мм. Для стабилизации управляемых колёс в среднем положении ось поворота колеса имеет поперечный и продольный наклоны (рис. 1.10.).
Колесо состоит из металлического обода и диска. У штампованных колёс диск с ободом соединяются посредством сварки. У литых и кованых колёс диск и обод выполнен за одно целое. На обод колеса монтируется шина. Шины бывают двух типов – камерные и бескамерные. По способу укладки несущего корда, различают шины радиальные и диагональные, а по форме и рисунку протектора – зимние, летние и всесезонные. Имеются и другие конструктивные различия шин.
Механизмы управления
К механизмам управления относятся рулевое управление и тормоза.
Рулевое управление обеспечивает изменение направления движения автомобиля путём поворота его управляемых колёс. Рулевое управление состоит из: 1) рулевого колеса с валом, установленным в рулевой колонке; 2) рулевого механизма; 3) рулевого привода и некоторых других деталей.
Рулевой механизм обеспечивает передачу усилий от рулевого колеса с валом на детали рулевого привода и далее на рулевую трапецию и управляемые колёса. Большее распространение имеют рулевые механизмы глобоидально-червячного и реечного типа.
К деталям рулевого привода легковых автомобилей с независимой передней подвеской относят рулевую сошку, маятниковый рычаг, среднюю и боковые рулевые тяги, рулевые наконечники, рулевые рычаги поворотных кулаков или стоек и другие детали. В устройстве привода рулевого механизма червячного или реечного типа имеются отличия.
Детали рулевого привода образуют рулевую трапецию. Рулевая трапеция осуществляет одновременный поворот управляемых колёс, при этом, внутреннее к центру поворота колесо должно поворачиваться на больший угол, чем внешнее, для обеспечения качения колёс по окружностям, описанным из одного центра. Следует различать нерасчленённые и расчленённые рулевые трапеции. Нерасчленённую трапецию применяют на автомобилях, у которых управляемые колёса устанавливаются на одной оси, подвешенной через детали подвески к кузову или раме. Расчленённую подвеску используют при независимой подвеске управляемых колёс. Рулевые управления с глобоидально-червячным механизмом и механизмом реечного типа показаны на рис. 1.11
Тормозные системы автомобиля служат для снижения скорости автомобиля и его остановки, а также для удержания автомобиля в неподвижном состоянии. Замедление автомобиля обеспечивает рабочая тормозная система. Удержание автомобиля в неподвижном состоянии на уклоне при остановке или стоянке обеспечивает стояночная тормозная система. Помимо перечисленных систем, которые можно назвать основными, автотранспортные средства оснащаются другими средствами для торможения. На грузовых автомобилях и прицепных устройствах находят применение аварийные, запасные, вспомогательные, а также различные типы моторных тормозных систем. Широкое распространение имеют антиблокировочные системы (ABS).
Управление рабочей тормозной системой осуществляется от ножной педали тормоза. Передача усилий от педали тормоза к рабочим тормозным механизмам реализуется через гидравлический, пневматический и редко механический привод. В автомобилях, оснащённых системами ABS, ASR и системами управления динамикой автомобиля тормозные усилия регулируются ЭБУ (электронными блоками управления). Электронные системы управления тормозами широко используется в электропневматических и электрогидравлических тормозных механизмах.
Основными узлами и деталями рабочей тормозной системы с гидравлическим приводом являются: 1) главный тормозной цилиндр с бачком для тормозной жидкости; 2) рабочие тормозные цилиндры, соединённые с главным тормозным цилиндром и регулятором тормозных усилий трубопроводами; 3) колёсные тормозные механизмы, состоящие из тормозных барабанов или дисков и тормозных колодок; 4) педаль тормоза и усилитель тормозов вакуумного или иного типа.
Стояночный тормоз имеет механический привод и при включении блокирует задние колёса автомобиля. В ряде устаревших конструкций стояночный тормоз воздействует на карданный вал (в настоящее время применение трансмиссионного стояночного тормоза запрещено Правилами ЕЭК ООН и ГОСТ РФ). На грузовых автомобилях с пневмотормозами стояночный тормоз приводится в действие при помощи энергоаккумулятора.
Общее устройство рабочей и стояночной тормозной системы легкового автомобиля показано на рис. 1.12

Корпус двигателя.
Поршневой двигатель внутреннего сгорания классической (традиционной) конструкции имеет корпус, состоящий из блока цилиндров (блок-картера) и головки блока цилиндров , закрытых, сверху - клапанной крышкой , снизу - масляным поддоном , спереди и сзади - передней и задней крышками коленчатого вала с самоподжимными сальниками. Корпус может иметь и иную конструкцию. Например, нижняя часть картера может быть разъёмной, и в этом случае корпус будет состоять из трёх составных частей: блока цилиндров (средней части корпуса), головки блока цилиндров (верхней части корпуса) и фундаментной рамы (нижней части корпуса) и соответствующих крышек. Встречаются двигатели с моноблочной конструкцией корпуса, в котором блок цилиндров и головка блока цилиндров выполняются в виде единой, неразъёмной отливки.Многообразие конструкций двигателей различных моторостроительных предприятий, предполагает различные подходы к их ремонту .
Корпусные детали двигателя являются основанием для крепления деталей кривошипно-шатунного и газораспределительного механизмов, а так же узлов и деталей систем смазки, охлаждения, зажигания, питания и др. Детали корпуса двигателя показаны на рис. 3.1.
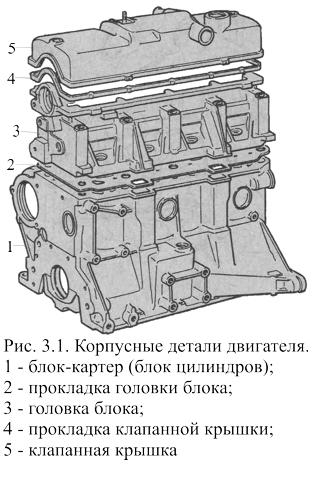
Блоки цилиндров отливаются из серого легированного чугуна или высококремнистых алюминиевых сплавов ( силуминов ). Некоторыми фирмами практикуется изготовление блоков из металлокерамики. Блоки цилиндров двигателя с жидкостным охлаждением имеют двойные стенки, образующие «рубашку охлаждения» . Рубашка охлаждения заполняется охлаждающей жидкостью.
Блоки цилиндров двигателей с воздушным охлаждением цилиндров имеют оребрение. Цилиндры, как правило, заключены в кожух, через который вентилятором системы охлаждения прокачивается воздух.
Головки блоков цилиндров бензиновых и дизельных двигателей легковых автомобилей отливаются из алюминиевых сплавов и реже из чугуна и, за редким исключением, имеют моноблочную конструкцию, т.е. на один ряд цилиндров двигателя устанавливается одна, единая для всех цилиндров, головка. На части дизельных двигателях каждый цилиндр (или пара цилиндров) может иметь собственную головку. Головка через термостойкую прокладку крепится к привалочной плоскости блока цилиндров болтами, если блок чугунный, или гайками через шпильки, если блок алюминиевый. Болты крепления головки изготавливаются из высокопрочных сталей и при небольших диаметрах должны обеспечивать значительные усилия (моменты) затяжки . Усилия затяжки болтов (гаек) крепления головки блока регламентируется производителем и, для большинства автомобилей, в среднем составляют 9, 0 – 10, 0 кгс x м. Стенки головки блока двойные. Рубашка охлаждения, образованная двойными стенками головки блока соединяется с рубашкой охлаждения блока цилиндров. В головке блока выполняются камеры сгорания. На головке размещают детали газораспределительного механизма, включая распределительный вал (валы), впускные и выпускные клапаны и детали привода клапанов.
3.2. Детали цилиндропоршневой группы (ЦПГ) и
кривошипно-шатунного механизма.
К деталям цилиндропоршневой группы двигателя относятся: цилиндры (гильзы цилиндров); поршни; поршневые кольца; поршневые пальцы (рис. 3.2).
К деталям кривошипно-шатунного механизма двигателя относятся: шатуны и крышки шатунов; коленчатый вал и крышки коленчатого вала и маховик. Часть двигателей с малым числом цилиндров (до четырёх) могут иметь балансирные валы, которые также следует относить к деталям КШМ.
Цилиндры. В рядных двигателях, если блок цилиндров отливается из чугуна, цилиндры изготавливаются совместно с блоком. В чугунных блоках многорядных двигателей и блоках выполненных из алюминиевых сплавов цилиндры могут изготавливаться в виде отдельных гильз из чугуна, специальной стали или металлокерамики.
Гильзы, которые устанавливаются непосредственно в рубашку охлаждения блока цилиндров, носят название «мокрых» . Наружная поверхность «мокрых» гильз омывается охлаждающей жидкостью. Мокрые гильзы устанавливаются в отверстия блока с зазором, и удерживаются от перемещения в этом отверстии головкой блока цилиндров. Для надёжного закрепления гильзы головкой блока цилиндров верхний бурт гильзы должен выступать за верхнюю плоскость блока на величину, регламентируемую техническими условиями (для разных типов двигателей эта величина лежит в пределах 0, 02 – 0, 12мм).
Гильзы, наружная поверхность которых не контактирует с охлаждающей жидкостью, носят название – «сухие гильзы». «Сухие» гильзы устанавливаются в блок с натягом. Сборка соединений с натягом означает, что диаметр втулки (гильзы) больше диаметра посадочного отверстия, в которое эта втулка устанавливается. Величина натяга измеряется в миллиметрах и определяется как разница диаметров сопрягаемых деталей. Натяг обеспечивает неподвижность гильзы при тепловом расширении материала блока в процессе прогрева работающего двигателя.
Внутренняя рабочая часть цилиндра обрабатывается на специальном оборудовании до определённой чистоты (шероховатости) и имеет ровную поверхность, которую называют « зеркалом цилиндра». При финишной (окончательной) обработке цилиндра на его поверхность наносятся пространственно ориентированные риски, способствующие удержанию в них масла нужного для смазки поршневых колец и поршней.
На рабочие поверхности алюминиевых цилиндров могут наноситься дополнительные покрытия типа «никасил» (никель с кремнием) или кремниевые покрытия, получаемые кислотным травлением поверхности. Рабочие поверхности чугунных цилиндров, как правило, термической обработке не подвергаются и покрытий не имеют. Технология ремонта алюминиевых и чугунных цилиндров может существенно отличаться.
По внутреннему диаметру цилиндры номинальных размеров разбиваются заводом изготовителем на категории (классы) с шагом 0, 01 мм. Категории цилиндров обозначаются обычно буквами латинского алфавита (A, B, C…..) и клеймятся на привалочной плоскости картера двигателя или ином месте. Класс (категория, группа) цилиндра, так же может обозначаться краской, цифрой, печатным оттиском, или другим способом.
На рис. 3.3а. показаны корпусные детали рядного шестицилиндрового двигателя, гильзованого мокрыми чугунными гильзами. На рис. 3.3б показан блок-картер рядного четырёхцилиндрового двигателя традиционной конструкции с цилиндрами, выполненными заодно с блоком.

Поршни изготавливаются из алюминия легированного кремнием и другими металлами методом литья в кокиль (специальная форма) или методом штамповки с последующей обработкой детали резанием. Для некоторых типов автомобильных двигателей, работающих с высокими удельными нагрузками на детали, поршни изготавливаются из стали и металлокерамики.
Поршни воспринимают давление газов, обеспечивают передачу усилий на шатун и герметизируют камеру сгорания.
Верхняя часть поршня носит название - головка поршня, нижняя направляющая часть поршня называется юбкой поршня. На рис. 3.4 показана конструкция поршня а) бензинового двигателя и б) дизельного двигателя с полураздельной камерой сгорания

Головка поршня – наиболее усиленная часть поршня, где толщина стенок может достигать нескольких мм. На головке поршня выполнены канавки под поршневые кольца. В нижней канавке маслосъёмного кольца прорезаются дренажные отверстия для отвода масла. В головку поршня, для повышения износостойкости поршня, могут заделываться чугунные вставки, а на днище поршня (верхняя часть головки) и зону «огневого пояса» (часть головки поршня от днища до канавки первого компрессионного кольца) наноситься специальные покрытия. Днище поршня может иметь плоскую, выпуклую, вогнутую и иную форму. В днище поршней части двигателей выполняются углубления под клапаны (цековки) или камеры сгорания.
Юбка поршня . Толщина стенок юбки современных поршней может быть меньше 1, 5 мм. Для лучшей приработки поршня в цилиндре на юбку поршня напыляют тонкий слой олова или графитовое покрытие. Для этих же целей на юбке поршня выполняют «накатку» в виде микроканавок глубиной до 0, 02 мм, в которых при работе двигателя удерживается масло. Юбки поршней двигателей с цельноалюминиевыми цилиндрами могут покрываться тонким слоем железа. В средней части юбки имеются отверстия под поршневой палец. Стенки юбки у отверстия под поршневой палец имеют утолщения (приливы), именуемые бобышками . У большинства поршней ось отверстия под поршневой палец смещена относительно плоскости симметрии поршня в сторону на 0, 5 – 2, 5 мм.
Поршни автомобилей российского, европейского и американского производства часто изготавливаются со стальными терморегулирующими вставками в юбке у отверстия под поршневой палец. Вставки, имеющие по сравнению с материалом поршня, меньший коэффициент теплового расширения, препятствуют расширению юбки поршня при нагревании. С той же целью уменьшения теплопередачи от головки поршня к юбке с наружной стороны бобышек выполняются подрезы, которые носят название «холодильников», а по нижней канавке маслосъёмного кольца или на юбке поршня, сквозные разрезы «Т» - или «П» – образной формы.
Юбка поршня в плане имеет форму овала, большая ось которого перпендикулярна оси отверстия поршневого пальца. В продольном разрезе поршень имеет форму конуса, расширяющегося к юбке. Эллипсность юбки и разница диаметров поршня в верхней и нижней его части может быть более 0, 50 мм.
Поршень устанавливается в цилиндр с зазором. Зазор должен компенсировать расширение поршня при нагревании и обеспечивать присутствие масла между трущимися деталями. Величина установочного зазора строго регламентируется заводом изготовителем и в зависимости от конструкции того или иного двигателя лежит в пределах 0, 01 – 0, 09 мм (большинство двигателей будут нормально работать с зазором 0, 04 – 0, 06 мм.). Установочный зазор между стенкой цилиндра и поршнем обеспечивается по большей оси овала юбки поршня.
Поршни для одного двигателя не должны отличаться по массе более чем на 2-4 грамма или не более чем на 1 -1, 5% среднего арифметического от суммы масс всех поршней данного двигателя.
Заводы выпускают поршни номинального и ремонтного размеров. По наружному диаметру и диаметру отверстия под поршневой палец поршни номинального размера, разбиваются на категории (классы). Информация о размерности и весе поршня, а так же иная информация, выбивается на днище поршня (рис. 3.5).
Поршневые кольца (рис. 3.6) изготавливаются из чугуна легированного никелем, хромом, молибденом и другими металлами или стали и выполняют следующие функции: 1).Уплотняют поршень в цилиндре; 2). Снимают излишки масла со стенок цилиндров; 3).Отводят тепло от поршня в стенки цилиндров.
Кольца имеют прямой вырез, называемый замком кольца. Замок позволяет кольцу пружинить.
На поршнях современных двигателей устанавливают по два – три кольца. По назначению кольца делятся на компрессионные кольца и маслосъёмные кольца. Компрессионные кольца устанавливаются в верхней части головки поршня и отвечают за уплотнение поршня в цилиндре. Маслосъёмные кольца устанавливаются под компрессионными кольцами и отвечают за снятие излишек масла со стенок цилиндров. Излишки масла через прорези в кольце и отверстия в поршневой канавке маслосъёмного кольца сбрасываются под поршень и далее стекают в картер двигателя. Маслосъёмные кольца – составные и имеют в своём составе непосредственно кольцо (или два кольца - диска) и пружинный расширитель.
Рабочую поверхность верхних компрессионных колец, работающих в условиях высоких температур и при недостатке смазки, покрывают слоем пористого хрома или молибденом для повышения износоустойчивости. Кромки рабочих поверхностей колец имеют сложную форму в связи с чем, кольца должны устанавливаться на поршень в строго определённом положении. Неправильная установка колец может привести к прорыву газов в картер двигателя, снижению компрессии и повышению расхода масла на угар. Для правильной установки кольца на поршень на верхней части кольца делается специальная метка («тор», «верх»). При отсутствии меток следует обратиться к инструкции завода-изготовителя колец.
Заводы выпускают в продажу кольца номинальных и ремонтных размеров. На верхнюю часть колец ремонтных размеров ставится цифровая маркировка (например, 40 или 80), соответствующая увеличению наружного диаметра кольца (цилиндра) на ремонтный размер (на 0, 4 или 0, 8 мм, соответственно).
Поршневые пальцы шарнирно соединяют поршень с шатуном. Поршневые пальцы изготавливаются из низкоуглеродистых сталей легированных никелем и хромом и представляют собой короткую стальную толстостенную трубку. Поверхность пальцев обрабатывается с высокой точностью и полируется. Для придания поверхности пальца необходимой прочности, поверхность закаливается токами высокой частоты, цементируется или азотируется.
По способу соединения поршневого пальца с верхней головкой шатуна и с поршнем различают поршневые пальцы плавающего типа и пальцы, запрессованные в верхнюю головку шатуна.
Пальцы плавающего типа устанавливаются в верхнюю головку шатуна через, запрессованную в отверстие головки, сталебронзовую, сталеалюминевую или бронзовую втулку. Между втулкой и пальцем должен быть зазор, величина которого регламентируется техническими условиями. В бобышки поршня палец вставляется с небольшим натягом. От осевого перемещения палец удерживается стопорными кольцами.
Пальцы, запрессованные в верхнюю головку шатуна, в бобышках поршня перемещаются свободно, а в головку шатуна устанавливаются со значительным натягом. Натяг должен обеспечивать неподвижное положение пальца при существенных нагрузках, действующих на детали.
По наружному диаметру пальцы подразделяются на классы, через 0, 004 мм. Класс маркируется краской на торце пальца или, если позволяет толщина стенки, цифрой или буквой.
Шатун передаёт усилие от поршня на коленчатый вал двигателя и совместно с валом преобразует поступательное движение поршня во вращательное движение вала. Шатуны изготавливаются из углеродистых сталей легированных марганцем, хромом, никелем, молибденом и др. металлами методом ковки в штампах с промежуточной и финишной термообработкой и обработкой резанием. Шатун является одной из самых нагруженных деталей в двигателе. Шатун состоит из стержня, имеющего двутавровое сечение, поршневой (верхней) и кривошипной (нижней) головок. Для установки на коленчатый вал, нижняя головка выполнена разъёмной и имеет крышку. Так как отверстие в нижней головке шатуна выполняется и обрабатывается в сборе с крышкой, крышки шатунов не взаимозаменяемы и устанавливаются на головку в строго определённом положении. Для правильной установки крышек на них и нижних головках шатунов выбиваются специальные метки. С этой же целью на привалочных плоскостях крышки и головки шатуна могут выполняться соединительные ступеньки (выступы). Крышка крепится к нижней головке шатуна шатунными болтами. Для обеспечения высокой прочности болтов для их изготовления используются специальные стали, особые технологии производства и обработки. Шатуны для одного двигателя не должны отличаться по массе более чем на 2-6 граммов (1 - 1, 5% среднего арифметического от суммы масс всех шатунов двигателя).
Коленчатый вал (КВ) через шатун воспринимает усилие от поршня. Крутящий момент, развиваемый на коленчатом валу, через механизмы трансмиссии передаётся на ведущие колёса автомобиля.
Коленчатые валы изготавливаются из высокопрочных легированных углеродистых сталей методом ковки или точным литьём из особого чугуна с шаровидным графитом.
Коленчатый вал состоит из коренных и шатунных шеек, соединяющих их щёк, а также противовесов, переднего носка и заднего фланца. Коренные и шатунные шейки со щеками и противовесами образуют колено. Для подачи масла к шатунным подшипникам в щеках вала от коренных шеек просверливаются специальные каналы. Каналы снабжаются грязеуловителями. Грязеуловители способствуют дополнительной центробежной очистке масла, поступающего к шатунной шейке, и представляют собой просверленный или отлитый в шатунной шейке горизонтальный или наклонный канал, выходы из которого закрыты заглушками. Смазка шеек вала принудительная под давлением. Места перехода шеек к щёкам называются галтелями. Для уменьшения вероятности поломки вала, галтели делают закруглёнными и по галтели выполняют радиусную канавку глубиной 0, 2 – 0, 5 мм. Канавка уменьшает напряжения в металле в зоне соединения щеки и шейки. При ремонте коленчатого вала (шлифовке шеек) глубина канавок и радиус закругления галтелей должны быть восстановлены. Коренными шейками вал устанавливают в опорах картера двигателя и закрепляют крышками. Крышки коленчатого вала не взаимозаменяемы и должны устанавливаться на опору только в одном положении. Вал с наибольшим числом опор из возможного их количества называется полноопорным. К шатунным шейкам коленчатого вала крепится шатун. В двигателях с V – образным блоком цилиндров на одну шатунную шейку коленчатого вала может крепиться два шатуна. На одну шатунную шейку может приходиться один или два противовеса. Противовесы служат для разгрузки коренных подшипников от действия моментов, создаваемых центробежными силами от вращающихся частей и сил инерции поступательно движущихся частей. Расположение кривошипов КВ и их число зависит числа и расположения цилиндров двигателя. В табл. 3.1 приведены схемы расположения кривошипов коленчатых валов разных двигателей и указан возможный порядок работы цилиндров двигателей.
Поверхности шеек чугунных коленчатых валов закаливаются токами высокой частоты, а стальных азотируются на глубину до 1, 50 мм для придания им прочности и износостойкости (ч исло ремонтов коленчатого вала зависит от глубины закалки его шеек). На передний носок КВ устанавливают шкив привода вентилятора и генератора, зубчатое колесо привода масляного насоса, звёздочку цепи, масляный отражатель и гаситель крутильных колебаний. На задний фланец КВ болтами или гайками через шпильки крепится маховик. Передний носок и задний фланец КВ уплотняется сальниками.
На рис. 3.7 показаны полноопорные валы четырёх и шестицилиндровых двигателей с полным и неполным числом противовесов. На рис. 3.8 показан фрагмент коленчатого вала V-образного двигателя с маховиком и деталями поршневой и шатунной группы.
Маховик обеспечивает равномерное вращение коленчатого вала при работе двигателя и представляет собой чугунный тщательно сбалансированный диск на обод которого надет стальной зубчатый венец для пуска двигателя от стартера. Маховик устанавливается на задний фланец коленчатого вала (рис. 3.8) в строго определённом положении, для чего болты крепления маховика расположены несимметрично, и центрируется. Для точного центрирования маховика служит бурт самого фланца, либо установочные штифты.
Подшипники коленчатого вала. Подавляющее большинство коленчатых валов
двигателей современных автомобилей вращаются в подшипниках скольжения - вкладышах . Коренные вкладыши устанавливаются в опоры и крышки коленчатого вала и центрируются в них с помощью замков. Шатунные вкладыши устанавливаются в постели крышки и нижней головки шатуна. Замок вкладыша представляет собой «усик» шириной до 4, 0 мм, отогнутый при изготовлении вкладыша. Основой вкладыша является стальная лента, на которую наносят слой антифрикционного материала (т.е. материала, уменьшающего трение), состоящего из алюминиевого сплава с различным содержанием свинца, олова, сурьмы, кремния и меди. Общая толщина вкладышей современных двигателей 1, 0 – 2, 5 мм. Во вкладыше выполняется канавка и/или отверстие для подвода масла к шейке коленчатого вала. Вкладыши разных двигателей по составу антифрикционного состава могут сильно отличаться. На рис. 3.8 показаны различные конструкции подшипников скольжения. Заводами изготовителями в запасные части поставляются вкладыши номинального и ремонтного размеров. Ремонтный размер вкладыша выбивается на его тыльной (не рабочей) поверхности.
От осевого перемещения коленчатый вал удерживается упорными подшипниками, выполненными в виде колец или полуколец и устанавливаемых в центральной или задней коренной опоре коленчатого вала. Материал, из которого изготавливаются упорные подшипники, идентичен материалу вкладышей.
Гораздо реже в автомобильном двигателестроении, для коленчатых валов применяют подшипники качения (шариковые, роликовые или игольчатые). Существенным преимуществом подобной конструкции является то, что подшипники качения не требуют смазки под давлением.
Детали клапанной группы.
К деталям клапанной группы относятся впускные и выпускные клапаны, сёдла клапанов, направляющие втулки клапанов со стопорными кольцами и уплотнениями клапана (сальниками клапана), клапанные пружины, тарелки, шайбы и конические разрезные «сухари» (рис. 3.12).
Клапаны. Основными элементами клапана являются головка и стержень. Клапаны изготавливаются из прутковой стали способом её высадки. Для изготовления впускного клапана применяют хромистую или хромокремнистую сталь. Выпускные клапаны работают в условиях высоких температур, и во избежание быстрого выгорания производятся из жаропрочных сильхромовых или хромоникельмарганцовистых сталей. При этом стержень и головка выпускных клапанов может изготавливаться из разных сталей и соединяться между собой сваркой. Стержень выпускного клапана иногда делается полый. Полость заполняется жидким металлическим натрием, который при работе клапана способствует переносу тепла от сильно нагретой головки клапана в стержень. Поверхность стержня шлифуют и иногда хромируют для повышения износоустойчивости. Рабочей поверхностью тарелки ( фаской ) клапан плотно прилегает к седлу, запрессованному в головку блока цилиндров.
Сёдла клапанов для алюминиевых головок блока выполняются из жаропрочного чугуна (реже стали) и устанавливаются в головку с натягом 0, 09 – 0, 12 мм с последующей завальцовкой материала головки на седло. Неплотная посадка клапана в седле, является основной причиной его выхода из строя (прогорания) и разгерметизации камеры сгорания.
Направляющие втулки клапанов изготавливаются из чугуна, бронзы или металлокерамики и запрессовываются в головку цилиндров блока (или в блок цилиндров, при нижнем размещении клапанов) с натягом 0, 04 – 0, 08 мм. Через направляющую втулку проходит стержень клапана. Втулка может иметь посадочный поясок для установки сальника клапана ( маслосъёмного колпачка ), уплотняющего стержень клапана и предотвращающего попадание излишек масла по стержню клапана в камеру сгорания. При этом для улучшения смазки стержня клапана, по внутренней поверхности направляющей втулки выполняют спиральную канавку («резьбу») с шагом 2 – 3 мм, в которой удерживается масло. Зазор между стержнем клапана и втулкой регламентируется изготовителем и для большинства двигателей устанавливается в пределах 0, 04 – 0, 08мм у впускных клапанов и 0, 06 – 0, 12мм у выпускных.
Пружины клапанов возвращают клапан на седло после снятия с него нагрузки от кулачка распределительного вала, удерживают клапан в закрытом положении, обеспечивая его плотную посадку в седле, и предотвращают разрыв кинематической связи между передаточными деталями и клапаном. На один клапан устанавливается одна или две пружины (внутренняя – малая, и наружная – большая). Витки большой и малой пружин имеют противоположную навивку. Пружина надевается на стержень клапана и закрепляется на его конце через опорную тарелку с помощью разрезных конических сухарей.
ВВЕДЕНИЕ В ДИАГНОСТИКУ.
Неисправности не возникают «вдруг» и сами по себе. Причины их появления могут быть различны. В процессе эксплуатации двигателя его детали изнашиваются, изменяется их геометрия, увеличиваются зазоры между парами трения. Износу «способствует» множество факторов: стиль вождения, условия эксплуатации, несвоевременное или/и неквалифицированное обслуживание, низкое качество горюче-смазочных материалов, работа с детонацией, калильным зажиганием, неисправными системами смазки и охлаждения и т.п. По мере износа двигателя его эксплуатация становится всё более обременительной, возрастают эксплутационные расходы, появляются проблемы в работе. Эксплуатация изношенного двигателя приведёт к его повреждению. Ремонт двигателя получившего повреждения требует б о льших капитальных вложений.
Прежде чем приступить к ремонту, необходимо 1) определить неисправность и 2) причину её возникновения. Задачей ремонта является устранение, как самой неисправности, так и её причин и следствий. Специалисты, занимающиеся диагностированием неисправностей должны обладать достаточной квалификацией, сводящей к минимуму возможные ошибки при диагностике. Работу специалиста-диагноста можно сравнить с работой врача, от правильного диагноза которого зависит не только успешное лечение пациента, но и его послеоперационное состояние и здоровье. «Набор» возможных неисправностей двигателя (как и любого другого узла и агрегата) не бесконечен. Этот «набор» отличается в зависимости от модели (конструкции) автомобиля и может быть «просчитан». По своей сути диагностические работы сводятся к последовательному выполнению ряда действий и специальных мероприятий, направленных на подтверждение или опровержение предположений о проявившей себя неисправности и причинах её появления. Важно, чтобы были рассмотрены действительно все возможные причины, была правильно определена очерёдность их рассмотрения (по принципу «от простого - к сложному») и применены наиболее действенные, для конкретного случая, методы диагностирования. Принцип «от простого - к сложному» - основополагающий в диагностике. Следование этому принципу позволит сократить время и издержки, а также избежать ошибок. Надеюсь, Вы согласитесь с тем, что полная разборка двигателя, слишком радикальный метод выяснения причины того, почему он не запускается. А вдруг он не запускается всего лишь по причине отсутствия топлива в топливном баке!?
Подытожим сказанное:
· Любая неисправность имеет причину возникновения (или несколько причин), задача диагностики состоит в их выявлении;
· При поиске неисправностей и причин их возникновения следует придерживаться определённой последовательности действий, руководствуясь принципом «от простого - к сложному».
· Диагностика предшествует любому ремонту и от того, как квалифицированно она выполнена, будет во многом зависеть качество ремонта, его стоимость и трудоёмкость. Результатом (конечным продуктом) диагностики является информация о неисправности. Данная информация используется для определения вида предстоящего ремонта (частичный или капитальный), технологии ремонта, планировании времени и затрат на его проведение.
Диагностирование может быть субъективным и объективным. Субъективное диагностирование осуществляется с помощью органов чувств и не сложных приборов, усиливающих тот или иной сигнал. К субъективному способу диагностирования относится, в том числе, и диагностика по внешним признакам. Объективное диагностирование выполняется при помощи стендов, приборов и контрольно-измерительного оборудования (инструментальная диагностика). Так же следует различать общую и углублённую диагностику. Общая диагностика позволяет оценить состояние узла или агрегата автомобиля в целом (т.е. исправен или не исправен), без указания конкретной неисправности. Углублённая диагностика выявляет не только неисправность, но и её причину.
Значительная часть возможных неисправностей механической части двигателя и, в меньшей степени, его систем может быть продиагностирована субъективно, по характерным, для той или иной неисправности, внешним признакам. При этом некоторые из этих неисправностей (в особенности механической части) не поддаются диагностированию иными методами (например, инструментальными) или диагностируются ими «неуверенно». Большую часть неисправностей систем зажигания, питания и других систем двигателя, наоборот, можно выявить только с помощью специального диагностического оборудования. Следует иметь в виду и то обстоятельство, что при определённых неисправностях двигатель невозможно запустить. В подобном случае ограничены возможности применения любого из названных методов.
5.1 Диагностика неисправностей по внешним признакам.
Работа неисправного двигателя характеризуется рядом внешних проявлений, выражающихся в изменении цвета выхлопных газов, наличии посторонних шумов и стуков, повышенном расходе эксплутационных жидкостей, ухудшении основных рабочих характеристик (мощности, крутящего момента) и др.
5.1.1 Диагностика по цвету выхлопных газов.
При работе исправного отрегулированного двигателя в тёплую погоду при нормальной влажности, выхлоп из глушителя бесцветный. Изменение цвета выхлопных газов может быть следствием неисправностей в механической части двигателя или его системах.
1. Сизый (голубовато-серый) дым выхлопа, как правило, свидетельствует о попадании моторного масла в камеру сгорания цилиндра сверх допустимой нормы. Масло сгорает вместе с рабочей смесью и в виде «сизого» дыма из глушителя выбрасывается в атмосферу. Чем больше масла попадает в цилиндры, тем интенсивнее «дымление» двигателя. Сгоревшее масло не возвращается в картер двигателя и уровень его со временем понижается. Снижение уровня приходится компенсировать, доливая масло в двигатель (между плановой заменой масла, долив масла в исправный двигатель, не требуется). То есть, одновременно с дымным выхлопом наблюдается и повышенный расход масла «на угар». Часть сгоревшего масла в виде нагара откладывается на днищах поршней, клапанах и свечах зажигания. Чрезмерное отложение нагара на деталях двигателя, часто является причиной появления калильного зажигания. Частицы нагара, смываемые с деталей маслом и топливом, попадают в зазоры между парами трения и, имея значительную твёрдость, ускоряют изнашивание деталей. Масло быстро темнеет и раньше времени теряет свою работоспособность. Наличие паров масла в топливной смеси ухудшает процесс сгорания, что снижает давление газов на поршень. Крутящий момент и мощность двигателя также снижаются.
Повышенное нагарообразование на поршнях, при неблагоприятных условиях работы (перегрузки, некачественное топливо и т.п.), может привести к детонации (нагар на поршнях увеличивает степень сжатия).
Отложение нагара на клапанах приводит к неплотной посадке клапана в седле. Вследствие того, что перенос тепла от тарелки клапана в седло ухудшается, клапан быстро (через 300 – 500 км.) прогорает. Прогар клапана, в свою очередь, влечёт за собой разгерметизацию камеры сгорания, снижение компрессии и иные не желательные последствия, о которых мы уже знаем.
Нагар, который откладывается на электродах свечей зажигания, является хорошим проводником электричества. Энергия, поступающая на свечи зажигания для воспламенения горючей свечи, «стекает» по нагару мимо электродов, что тоже вносит свою лепту в копилку неисправностей двигателя.
Как мы видим, наряду с дымным выхлопом из глушителя, могут наблюдаться и иные проявления «неправильной» работы двигателя (повышенный расход масла, отложение нагара на деталях и т.п.), зачастую указывающие на одну и ту же неисправность и, в конечном счёте, являющиеся её следствиями. В свою очередь, эти следствия могут стать причинами неисправностей «второго порядка». Например, повышенное отложение нагара на клапане – следствие попадания масла в камеру сгорания, и при этом, – причина неплотной посадки клапана в седло, что рано или поздно, явится следствием его (клапана) прогорания. «Незаконное» проникновение «лишнего» масла в цилиндр, тоже имеет свои причины. Разобраться в хитросплетении причин и следствий, даже опытному мастеру, иногда бывает достаточно сложно. Поэтому имеет смысл придерживаться ещё одного правила: «Достоверность диагностики повышается пропорционально выявленным признакам, явно или косвенно указывающим на предполагаемую причину неисправности»
и подытожим:
· В рассматриваемом случае, дымление двигателя является следствием попадания моторного масла в камеру сгорания;
· Наряду с дымным выхлопом из глушителя, на ту же самую причину (попадание масла в камеру сгорания), прямо или косвенно могут указывать:
§ Повышенный расход масла на угар;
§ Отложения нагара на деталях двигателя и свечах зажигания;
§ Ухудшение рабочих характеристик двигателя;
§ Иные признаки (о которых мы поговорим ниже).
Основными причинами попадания масла в камеру сгорания двигателя могут быть:
a. Износ цилиндропоршневой группы в целом или маслосъёмных колец в частности;
b. Поломка деталей ЦПГ (колец, поршня, перемычек между кольцами на поршнях и т.п.), а так же задиры и царапины на зеркале цилиндра и юбке поршней, а так же коксование маслосъёмных колец в канавках поршня;
c. Износ маслосъёмных колпачков (сальников) клапанов, направляющих втулок клапанов и стержней клапанов;
d. Износ уплотнений вала турбокомпрессора (для двигателей с турбонаддувом).
Как много можно рассказать о двигателе, работающем с дымным выхлопом даже не заглядывая ему под капот. И масло он потребляет, и пробег у него наверняка «солидный», и изношен он сверх меры. А если ещё и возможные причины дымления перечислить! На непосвященных Ваш рассказ произведёт неизгладимое впечатление. Но полученное нами удовлетворение будет не полным, если из приведённого перечня возможных причин мы не выделим истинную причину. Но как это сделать? И можно ли это сделать, рассматривая только внешние признаки неисправностей? Отвечаем: В каких-то случаях можно, в других случаях придётся призвать на помощь инструментальную диагностику, а в исключительных случаях, истинную причину неисправности, как и саму неисправность, покажет только «вскрытие» (т.е. разборка двигателя).
а). Износ деталей ЦПГ «в целом» чаще всего происходит естественным путём. То есть детали изнашиваются постепенно в течение достаточно длительного периода эксплуатации. Логично предположить, что ко времени выработки двигателем своего ресурса, наряду с износом деталей ЦПГ, изношенными могут оказаться и другие детали (так и происходит на самом деле). При этом, одновременно с дымным выхлопом и повышенным расходом масла на угар, могут наблюдаться такие характерные признаки «приближающейся старости», как:
· Низкое давление масла в системе смазки, вызванное износом шеек КВ и их вкладышей;
· Повышенное давление картерных газов, вызванное прорывом рабочих и отработавших газов в картер двигателя через зазоры между изношенными деталями ЦПГ;
· Попадание масла в корпус воздушного фильтра воздухоочистителя и на вход двигателя через систему вентиляции картера, вследствие повышенного давления картерных газов. При этом, загрязнение воздушного фильтра маслом, в свою очередь, может стать причиной неустойчивой работы двигателя из-за переобогащения топливно-воздушной смеси («замасленный» фильтр плохо пропускает воздух);
· Посторонние шумы и стуки при работе двигателя, прослушиваемые в определённых зонах двигателя и вызванные увеличенными зазорами в сопряжении изношенных деталей или ослаблением посадок и креплений (см. раздел 5.1.2 «Диагностика по шумам и стукам»);
· Низкая компрессия во всех цилиндрах двигателя из-за износа деталей ЦПГ (см. раздел 5.2 «Инструментальная диагностика).
Имея «в наличии» такой «букет болезней» (или даже часть этого букета), наряду со значительным пробегом автомобиля, можно с достаточной уверенностью говорить о существенном износе двигателя и готовиться к его капитальному ремонту.
b ). Поломки деталей ЦПГ происходят по причинам отличным от причин естественного износа, в процессе которого детали всех цилиндров двигателя изнашиваются более или менее равномерно и одинаково. Поломки возникают вследствие: 1) неграмотной эксплуатации в т.ч. эксплуатации сильно изношенного двигателя; 2) попадания в цилиндр инородных предметов; 3)
неисправности систем двигателя (смазки, охлаждения); 4) неквалифицированно выполненного ремонта.
Так как весьма маловероятно, что одновременно сломаются или закоксуются кольца сразу во всех цилиндрах двигателя, или произойдёт задир зеркала всех цилиндров, то в качестве основной причины появления дымного выхлопа здесь следует рассматривать неисправность одного – двух цилиндров, а не двигателя в целом. При этом:
· Будут отсутствовать, уже названные нами, признаки «старости» двигателя;
· Пробег автомобиля не будет критическим;
· Измеренная компрессия будет низкой только в неисправных цилиндрах;
· Забрасываться маслом будут свечи только неисправных цилиндров;
· При «закорачивании» на массу свечи неисправного цилиндра, дымность выхлопа будет снижаться.
Поиск «неисправного цилиндра» «закорачиванием» на массу свечи зажигания (принудительным отключением цилиндра) давно известный и, можно сказать классический, метод диагностики, основанный на том, что при обесточивании свечи одного из цилиндров работающего двигателя, обороты КВ двигателя падают, если цилиндр исправен, и не изменяются (или изменяются несущественно), если цилиндр не работает (или работает с перебоями). Аналогичным способом определяют цилиндр «виновный» в наличии дымного выпуска или посторонних шумов и стуков. Причины неработоспособности самого цилиндра (неисправная свеча зажигания или высоковольтный провод, прогоревший клапан или сломанные кольца и т.п.), определяются отдельно.
Следует особо отметить не безопасность применения данного метода диагностики на современных автомобилях, имеющих системы управления зажиганием, в случае если «закорачивание» свечи осуществляется старым «дедовским» способом, т.е. путём отсоединения от неё высоковольтного провода. На сегодняшний день, данный способ применим лишь для двигателей оборудованных классическими контактными системами зажигания. Для всех других систем разрыв в цепи вторичного напряжения при работающем двигателе приведёт к выходу из строя электрического оборудования (датчиков, ЭБУ, модуля зажигания и т.п.). Данное предостережение не означает, что описанный метод совсем не подходит для современных автомобилей. Просто существуют другие, более безопасные способы «отключения» свечей зажигания, как с помощью электронных диагностических приборов и комплексов, так и «вручную», при отсутствии таковых.
c ). Износ и старение (потеря эластичности) маслосъёмных колпачков (сальников) клапанов наступает после 80 - 100 тысяч км. пробега и, как правило, происходит задолго до того как двигатель выработает свой ресурс (200 – 250 тысяч км.). Внешние проявления в работе двигателя, вызванные износом сальников клапанов и деталей ЦПГ весьма схожи, но при диагностике этих неисправностей, ошибка в установлении истиной причины нежелательна (замена колпачков занимает около полутора часов работы, замена изношенных деталей ЦПГ с расточкой цилиндров – это уже капитальный ремонт двигателя). Избежать подобной ошибки можно, оценив компрессию в цилиндрах двигателя (см. раздел 5.2.1). Дополнительно, на износ маслосъёмных колпачков прямо или косвенно могут указывать следующие признаки:
· Усиление дымного выхлопа при перегазовках двигателя;
· Наличие моторного масла на резьбовой части вывернутой свечи зажигания;
· Наличие тёмных полос нагара на корпусе подшипников распределительного вала или клапанной крышке (не всегда) напротив клапана, чей колпачок «пропускает» (в цилиндр колпачок пропускает масло, из цилиндра – отработавшие газы, которые и оставляют след на корпусе подшипников);
· Повышенный расход масла на угар.
Износ направляющих втулок клапанов и стержней клапанов сверх допустимых значений, так же приводит к попаданию масла в цилиндры двигателя, чему, зачастую не могут препятствовать, даже исправные сальники клапанов. Так как износ этих деталей, большей частью, происходит естественным образом, одновременно изнашиваются и другие детали двигателя. О «букете болезней», сопровождающих изношенный двигатель, мы уже говорили.
d ). Износ уплотнений вала турбокомпрессора приводит к значительному увеличению расхода масла на угар и работе двигателя с густым сизым дымом из-за попадания большого количества масла через патрубки турбокомпрессора в цилиндры двигателя. При измерении компрессии в цилиндрах, её величина может существенно превышать норму, из-за «уплотнения» маслом зазоров между парами трения деталей ЦПГ. Возникают проблемы с запуском и работой бензинового двигателя, вследствие забрасывания маслом свечей зажигания. При аварийном выходе из строя уплотнений вала турбокомпрессора или его подшипников в цилиндре двигателя возможен гидроудар.
Гидроудар происходит вследствие поступления в цилиндр большого количества масла, объём которого превышает объём камеры сгорания. Поршень, движущийся к ВМТ в конце такта сжатия «ударяется» о масло (жидкость не сжимаема) и двигатель останавливается. Шатун того цилиндра, где произошёл гидроудар, как правило, деформируется по оси. Повреждения могут получить и другие детали двигателя. К гидроудару больше «склонны» дизельные двигателя, имеющие малый объём камер сгорания.
Гидроудар возможен и при попадании в цилиндры воды, например, при преодолении водных преград.
2. Серый или чёрный цвет выхлопных газов, как правило, указывает на неполное сгорание топлива в цилиндрах двигателя.
Несгоревшее топливо, в виде копоти, осаждается на деталях двигателя (днищах поршней, электродах свечей зажигания и накаливания, клапанах) и в виде чёрного дыма выбрасывается в атмосферу. В выхлопных газах значительно возрастает доля вредных примесей (в основном СО, СН и С), ощущается характерный запах «несгоревшего топлива». Характеристики двигателя (мощность, крутящий момент, экономичность) ухудшаются. Работа бензинового двигателя, при этом, может сопровождаться «выстрелами» из глушителя с выбросом пламени.
Причина «выстрелов» - в парах несгоревшего топлива, вместе с отработавшими газами, попадающими из цилиндров в выпускной трубопровод и через него в атмосферу. На выходе из глушителя пары, имеющие высокую температуру, смешиваются с атмосферным воздухом, и самовоспламеняются. При неисправной («прогоревшей») системе выпуска, воспламенение паров несгоревшего топлива может происходить непосредственно внутри неё, что часто является причиной разрушения системы выпуска.
Неполное сгорание топлива неблагоприятно отражается и на работе каталитического нейтрализатора выхлопных газов, который может получить отравление парами топлива и выйти из строя. Выход нейтрализатора из строя приводит к проблемам в работе двигателя, вплоть до невозможности его запуска вследствие значительного возрастания сопротивления выпуску.
«Отравление» каталитического нейтрализатора не избежать, если заправлять автомобиль этилированным топливом (т.е. бензином, содержащим тетраэтилсвинец). Тетраэтилсвинец является сильным антидетонатором. Несмотря на высокую токсичность этилированного бензина, добавление в топлива этиловой жидкости практикуется рядом производителей и автозаправочных станций с целью повышения октанового числа топлива.
Итак:
· В рассматриваемом случае, дымление двигателя является следствием неполного сгорания топлива;
· Наряду с дымным выхлопом из глушителя, на ту же самую причину (неполное сгорание топлива), прямо или косвенно могут указывать:
§ Характерный запах несгоревшего топлива из глушителя (может ощущаться даже при отсутствии видимого выхлопа);
§ Повышенное содержание СО, СН и С в отработавших газах (определяется газоанализатором);
§ Повышенный расход топлива;
§ Наличие «печного» нагара (т.е. сажи) на свечах зажигания;
§ Возможный затруднённый запуск двигателя, неравномерная работа двигателя на режиме холостого хода и ухудшение его рабочих характеристик;
§ «Выстрелы» в глушителе
Наиболее вероятными причинами появления дыма серого – чёрного цвета могут являться:
a. Неисправности в системе питания двигателя;
b. Неполное закрытие или прогорание выпускных клапанов;
c. Неисправности в системе наддува двигателей.
a ). Неисправности в системе питания двигателя наиболее частая причина неполного сгорания топлива.
Двигатель работает на топливно-воздушной смеси, состоящей из паров топлива и воздуха, смешанных в определённой пропорции (воздух содержит кислород, необходимый для горения топлива). Для полного сгорания одной весовой части топлива (пусть этой весовой единицей будет килограмм) требуется примерно 14, 7 весовых частей (килограмм) воздуха. Состав смеси, состоящий из одного кг топлива и 14, 7 кг воздуха (1: 14, 7), называется стехиометрическим составом. Топливно-воздушная смесь, содержащая относительно большую часть топлива (или меньшую часть воздуха), считается богатой смесью и на сгорание всего топлива, имеющегося в данной смеси, не хватает воздуха (свободного кислорода). Несгоревшее топливо, в виде чёрного дыма (сажи), выбрасывается через систему выпуска автомобиля в атмосферу.
Причин, по которым система питания готовит богатую смесь достаточно много. Обобщённо проблема выглядит следующим образом. Либо в должном количестве в систему не подаётся воздух (например, загрязнён воздушный фильтр или воздушные жиклёры, неисправен датчик-расходомер воздуха системы управления двигателем и т.п.), либо с переизбытком поступает топливо (например, негерметичны топливные форсунки, разрегулирована система холостого хода и т.п.).
Так как в задачу данного пособия не входит подробное рассмотрение неисправностей систем двигателя, в том числе и систем питания, для более подробного ознакомления с затронутой темой мы отсылаем читателя к другим изданиям профильного направления.
b ). Неполное закрытие клапанов возможно по причине: 1) отложений на стержне и тарелке клапана большого количества нагара, препятствующего плотной посадке клапана в седло (нагарообразование на клапанах является следствием попадания масла в камеру сгорания через неисправные маслосъёмные колпачки); 2) износа рабочих поверхностей тарелки клапана и седла; или 3) из-за отсутствия зазоров в приводе клапанов (напомним, что величина этих зазоров регламентируется производителем и подлежит контролю и регулировке с периодичностью ТО – 2).
Неполная посадка клапана приводит к снижению компрессии в цилиндре и цилиндр частично или полностью выключается из работы. Как следствие, двигатель работает с перебоями, его рабочие характеристики ухудшаются, свечи в неработающем цилиндре холодные (в цилиндре нет горения смеси) и мокрые («забрасываются» топливом).
Прогар клапана приводит к выключению цилиндра из работы. При значительном повреждении клапана, компрессия в цилиндре стремится к нулю. Так как одновременное прогорание клапанов в нескольких цилиндрах маловероятно, то в других (исправных) цилиндрах, величина компрессии должна соответствовать норме.
c ). К неисправностям системы наддува двигателя, приводящим к появлению дымного выхлопа, можно отнести заклинивание вала турбокомпрессора или неисправности в приводе компрессора. Неисправности диагностируются визуально.
3. Выхлопные газы белого цвета свидетельствуют о наличие в их составе паров воды.
В сырую и холодную погоду выхлоп белого цвета не является признаком неисправности двигателя. Причиной его появления становится конденсат, образующийся в системе выпуска из-за разницы температур отработавших газов и атмосферного воздуха. Если этот конденсат и приносит вред, то только самой системе выпуска.
Наличие водяного пара в выпускных газах при положительной температуре и нормальной влажности воздуха, может указывать на невысокое качество залитого в бак топлива (содержит воду), или на попадание охлаждающей жидкости в цилиндры двигателя. В первом случае иногда можно наблюдать, как вода вытекает из глушителя буквально ручьём. Вода вызывает коррозию топливопроводов, плунжерных пар топливного насоса высокого давления дизелей, форсунок, других деталей системы питания и деталей двигателя. При отрицательных температурах вода, содержащаяся в топливе, может замёрзнуть в корпусе топливного насоса и стать причиной отказа двигателя запускаться.
Воду из топливного бака удаляют, открутив сливную пробку, ввёрнутую в дно бака, и спустив отстой. Топливные фильтры дизельных двигателей имеют отстойники, также оборудованные сливной пробкой. Если количество воды в топливе незначительно, его можно удалить, добавляя в топливо специальные (как правило содержащие спирт) присадки, связывающие воду, или чистый спирт из расчёта 100 мл. спирта на 10 литров топлива. Частично связывают воду и моющие присадки для топливных систем. Профилактическое использование топливных присадок целесообразно использовать не реже чем через 5000 км. пробега.
Попадание охлаждающей жидкости в цилиндры двигателя. Одной из основных причин попадания охлаждающей жидкости в цилиндры двигателя традиционной конструкции, является прогорание прокладки между головкой блока и блоком цилиндров двигателя. Причиной же самого прогорания является негерметичность стыка между этими корпусными деталями, возникающая либо из-за уменьшенного момента затяжки болтов (гаек) крепления головки блока, либо из-за деформации привалочных плоскостей. В свою очередь, деформация плоскостей случается вследствие сильного перегрева двигателя, или серий перегревов. Нарушение теплопередачи между «несостыкованными» корпусными деталями двигателя и прорыв в стык отработавших газов, имеющих высокую температуру, приводят к повреждению прокладки.
В качестве дополнительных признаков, указывающих на попадание охлаждающей жидкости в цилиндры двигателя, могут быть:
· Снижение уровня охлаждающей жидкости в системе охлаждения;
- Наряду с дымным выхлопом, из глушителя выбрасываются капли (брызги) охлаждающей жидкости.
Чтобы определить, что же в действительности выбрасывается из глушителя, конденсат или охлаждающая жидкость, можно проверить «состав», этой жидкости на ощупь ( осторожно, жидкость горячая). Антифризы на основе этиленгликоля маслянисты на ощупь и сладковаты на вкус ( осторожно, содержащийся в «Тосоле» этиленгликоль – ядовит).
Органолептический способ диагностики (т.е. на нюх, на вкус, на ощупь) сложно рекомендовать к применению. Он не совсем гигиеничен и, если не соблюдать элементарных правил и норм «здравого смысла» может быть опасен для здоровья. В тоже время, это старый и испытанный временем способ, имеющий место в повседневной практике, и использующийся для подтверждения (или опровержения) некоторых предположений. Данный способ, может быть, применим, и в тех случаях, когда другие способы диагностирования недоступны.
- Появление пузырьков воздуха в расширительном бачке системы охлаждения при работающем двигателе.
Через прогар в прокладке головки блока, образующийся между цилиндром и протокой рубашки охлаждения, в цилиндр попадает охлаждающая жидкость, а из цилиндра в рубашку охлаждения рабочие и отработавшие газы в виде пузырьков всплывающие в расширительном бачке и радиаторе системы охлаждения. Сильное повреждение прокладки головки блока и значительный выход газов в рубашку охлаждения приводит к «закипанию» охлаждающей жидкости и перегреву двигателя;
· Появление запаха отработавших газов из расширительного бачка радиатора;
· Увеличение уровня масла в картере двигателя, изменение цвета масла до светло-жёлтого или коричневато-жёлтого и образование водно-масляной эмульсии.
На работающем двигателе, попадающая в цилиндры охлаждающая жидкость вместе с отработавшими газами выбрасывается в атмосферу в виде водяного пара. На неработающем двигателе охлаждающая жидкость через зазоры между деталями цилиндропоршневой группы просачивается в картер, где, имея плотность большую, чем у масла, опускается на дно поддона картера, а при запуске двигателя смешивается с маслом с образованием эмульсии. Эксплуатация двигателя на эмульсии приведёт к повреждению деталей КШМ и ГРМ. Эмульсия в виде «пены» светло-жёлтого цвета может наблюдаться и на крышке маслозаливной горловины. На измерительном щупе, как правило, заметны капельки воды.
Причиной попадания охлаждающей жидкости в масло, может быть и наличие трещин в рубашке охлаждения двигателя или повреждение (например, коррозия) внутренних технологических заглушек, той же рубашки охлаждения. При наличии трещин и повреждении заглушек, возможно не только попадание охлаждающей жидкости в масло, но и масла в систему охлаждения, с образованием эмульсии, в том числе и в радиаторе. Подобная картина может наблюдаться также при повреждении промежуточного охладителя масла (для двигателей с охладителем масла).
- Неустойчивая работа двигателя.
Цилиндр двигателя, в который поступает охлаждающая жидкость, частично (если количество поступающей жидкости невелико) или полностью выключается из работы. Свечи зажигания (накаливания) в таких цилиндрах холодные и мокрые («забросаны» охлаждающей жидкостью).
5.1.2 Диагностика неисправностей по шумам и стукам.
Мы живём в океане звуков. Всё что, так или иначе, движется и перемещается в пространстве, пусть даже на микроскопические расстояния, производит свой звук в характерной только данному предмету тональности, продолжительности, громкости, интенсивности и области спектра. Человеческое ухо воспринимает далеко не весь спектр звуков, издаваемых окружающими нас объектами. Характер звуков огромного числа предметов столь же индивидуален, сколь индивидуален рисунок сетчатки глаза или, например, голос человека. И, как по голосу, или по шуму шагов на лестничном марше, Вы распознаёте близкого или хорошо знакомого Вам человека, как врач, по хрипам в лёгких ставит диагноз завзятому курильщику, так и обученные специалисты, по шумам и стукам, могут определять неисправности двигателя.
Обращаю Ваше внимание на то, что при диагностике неисправностей речь идёт о нехарактерных для двигателя (или иного агрегата) шумах и стуках, т.е. о звуках, появление которых, вызвано неисправностью каких либо деталей, механизмов или систем.
Источники шума работающего двигателя многообразны. Это и звук, впрыскиваемого форсунками топлива, и, всасываемого двигателем воздуха, и, взаимодействующих друг с другом деталей. С шумом, издаваемым двигателем, борются конструкторы и производители. На законодательном уровне большинства развитых стран, приняты законы, ограничивающие предельный уровень шума автотранспортных средств. Но создать совершенно бесшумный двигатель так же не реально, как изобрести вечный (хотелось бы ошибиться).
Шумность двигателя увеличивается по мере износа его деталей, из-за поломки деталей или неисправности отдельных систем и механизмов. По большей части, шумы и стуки являются следствием увеличения зазоров в сопряжении деталей, ослабления посадок и креплений. Диагностика неисправностей, проявляющих себя в виде посторонних шумов, имеет ряд существенных сложностей, и специалистов, владеющих и грамотно пользующихся данным методом, не так много.
При прослушивании двигателя следует определить:
· Источник звука (стука);
· Характер стука (регулярный или нерегулярный, периодический);
· Частоту стука относительно частоты вращения коленчатого или распределительного вала (большая, меньшая или равная);
· Зависимость интенсивности стука (увеличивается, уменьшается или не зависит) от нагрузки, частоты вращения валов и температуры двигателя;
· Тональность звука.
Полученная на основе прослушивания информация анализируется и сопоставляется с данными, полученными иными способами диагностирования. На основе сопоставления данных и анализа имеющихся признаков, делаются выводы о причинах появления стуков и возможных неисправностях.
Для прослушивания двигателя используют стетоскоп (прибор, которым врачи прослушивают лёгкие и сердце пациента). Автомобильный стетоскоп представляет собой длинную (около одного метра) слуховую трубку, со слуховым приспособлением мембранного типа (или просто «воронкой») на одном конце, и «мундштуком», прикладываемым к уху, на другом. При отсутствии специализированного стетоскопа можно пользоваться медицинским, или сухой деревянной палочкой, один конец которой прикладывается к прослушиваемому месту, а другой к уху.
Медицинский стетоскоп может показаться Вам очень «громким». Прослушивать через него работающий двигатель, работа сама по себе не из лёгких. Есть специалисты, которые предпочитают «слушать ртом», зажимая конец тонкой «слуховой» палочки зубами. Это не шутка. Попробуйте, вдруг получится.
Двигатель прослушивается в нескольких, условно выделенных зонах (рис. 5.1).

· В зоне 1, расположенной вдоль оси крепления коленчатого вала, прослушиваются коренные подшипники коленчатого вала;
· В зоне 2, расположенной немногим выше зоны 1 (на длину кривошипа КВ), прослушиваются стуки шатунных подшипников;
· В зоне «верхней мёртвой точки» (зона 3) прослушивается стук поршней и поршневых пальцев
· В зоне 4, лежащей вдоль оси крепления клапанной крышки, прослушивается распределительный вал (при верхнем размещении РВ на двигателе) и детали привода клапанов;
· В зоне 5, в передней части двигателя, прослушивается привод распределительного вала.
В зависимости от конструктивных особенностей двигателя число зон и их расположение может быть иным.
Стоит напомнить, что наибольшие нагрузки детали КШМ испытывают при прохождении через мёртвые точки и, в первую очередь, через верхнюю мертвую точку в начале такта рабочего хода. Так как появление посторонних стуков связано с увеличенными зазорами в сопряжениях деталей то, очевидно, что «слушать» нужно как раз в тех «зонах», где детали «проходят» через мёртвые точки.
Каждая неисправность имеет своё звучание. Но мы не станем останавливаться на словесном описании звучания изношенных деталей или деталей получивших повреждения. Для восприятия звука, звук должен быть услышан, и только в этом случае станут понятны такие словесные определения звука, как металлический, глухой, звонкий, тикающий, стучащий, высокий, низкий, дребезжащий и т.п. Не услышав звук, перечисленные определения останутся всего лишь словами, а слова без понимания сущности бессмысленны и, в конкретном случае, не имеют под собой практической основы.
Тональность и интенсивность звука, как правило, изменяется, или звук исчезает при принудительном выключении из работы неисправного цилиндра. Данный приём, во многих случаях, позволяет локализовать неисправность, и уже был описан нами ранее.
Разборка двигателя.
Разборка двигателя проводится в последовательности установленной заводом изготовителем. Описание последовательности разборки двигателя конкретной модели можно найти в сервисной литературе. Разборку двигателей традиционной конструкции обычно начинают со снятия навесных агрегатов, впускных и выпускных коллекторов, шкива коленчатого и распределительного валов и маховика. Затем снимают клапанную крышку, переднюю и заднюю крышки коленчатого вала, корпус подшипников РВ с распределительным валом (при верхнем расположении РВ) и головку блока цилиндров. Переворачивают двигатель вверх крышкой картера (масляного поддона), откручивают его, снимают маслоприёмный патрубок масляного насоса и масляный насос в сборе, отсоединяют крышки крепления шатунов от КВ и выталкивают поршни в сборе с шатунами из цилиндров. При наличии износного уступа в верхней части цилиндра, который может помешать выниманию поршней с шатунами из цилиндра, уступ срезают шабером (специальный инструмент). После вынимания поршней с шатунами откручивают болты крепления крышек коренных подшипников и снимают коленчатый вал двигателя. Если блок двигателя гильзован – выпресовывают гильзы.
В зависимости от конструкции двигателя возможен иной порядок разборки. В зависимости от вида ремонта возможен и иной объём разборочных работ (например, не имеет смысла снимать впускной и выпускной коллекторы, если не проводятся работы по ремонту самой головки блока цилиндров, или если они этому ремонту не мешают, и т.п.).
Перед началом разборки целесообразно совместить метки фаз газораспределения и другие установочные метки на валах и корпусных деталях двигателя для их идентификации (на шкивах может иметься несколько меток, в которых при последующей сборке двигателя можно запутаться). При невозможности определить местонахождение данных меток, поршень первого цилиндра двигателя следует поставить в верхнюю мёртвую точку на такте сжатия и повторить попытку. Если метки не найдены (редкий случай) промаркируйте шкивы любым доступным способом (например, нанесите метки кернером или краской) и при последующей сборке двигателя пользуйтесь ими.
В процессе разборки двигателя внимательно осматривайте детали. Детали, имеющие повреждения выбраковываются. Детали, не имеющие видимых повреждений, моются и откладываются для последующего инструментального контроля. Детали не получившие повреждений и не имеющие предельного износа, впоследствии могут быть установлены в двигатель повторно. Детали, которые планируется повторно устанавливать в двигатель должны быть помечены по месту установки. При сборке двигателя эти детали должны быть установлены на прежние места в прежней ориентации в пространстве (т.е, гильзы устанавливаются в свои гнёзда, поршни устанавливаются в свои гильзы, пальцы и кольца в свои поршни, клапаны в свои направляющие втулки и т.д.) В этом случае не нарушается сбалансированность двигателя и приработка деталей друг к другу.
К не изнашиваемым деталям двигателя относятся шатуны. Если шатуны не получили повреждений они повторно устанавливаются в двигатель.
Шатун не является парой трения для ответной детали поскольку шейки КВ и поршневой палец скользят по поверхности вкладышей, установленных в головках шатуна, при этом сами головки износу не подвержены.
Крышки шатунов и коренных подшипников не взаимозаменяемы (их нельзя путать местами). При снятии крышек проверяйте наличие на них меток и соответствие этих меток местам установки крышек. При отсутствии меток на крышках, крышки маркируются. После вынимания из двигателя поршня в сборе с шатуном установите снятую крышку на место и зафиксируйте её гайками. В этом случае крышки будет трудно перепутать с крышками шатунов других цилиндров и крышками шатунов с других двигателей.
При выполнении разборочных операций пользуйтесь исправными инструментами и приспособлениями (впрочем, это общее правило, актуальное для всех видов выполняемых работ).
Дефектация деталей.
Вымытые и очищенные детали осматривают, измеряют и сортируют на 1) годные, 2) подлежащие восстановлению и 3) негодные. Годные детали при сборке двигателя устанавливаются на прежние места с прежней ориентацией в пространстве. Детали, подлежащие восстановлению, ремонтируются и, так же, повторно устанавливаются в двигатель. Детали, не подлежащие ремонту, утилизируются. Контрольно-сортировочные операции требуют от исполнителя тщательности, внимания и терпения. Для выполнения инструментального контроля размеров и геометрии деталей необходимо иметь измерительный инструмент. Минимально-необходимый набор измерительных инструментов должен включать: 1) штангенциркуль для измерения размеров деталей и глубин отверстий с точностью измерения до десятых долей мм; 2) комплектмикрометров с общим диапазоном измерений от 0 до 100 мм, для измерения диаметров валов, длинны и толщины деталей с точностью до сотых долей мм; 3) нутромер, для измерения диаметров и деформаций отверстий с точностью до сотых долей мм; 4) комплектщупов от 0, 01 до 1, 00 мм, для измерений зазоров в сопряжении деталей; 5) слесарную линейку длиной не менее 30 мм; лекальную линейку и лекальный угольник для контроля неплоскостности поверхностей деталей; и стальную поверочную плиту.
На изношенном двигателе могут наблюдаться следующие неисправности деталей:
- Изменение размеров детали;
- Изменение геометрической формы детали, в т.ч. деформации плоскостей;
- Отклонения в точности взаиморасположения деталей;
- Механические повреждения;
- Трещины;
- Коррозия деталей;
- Изменение физико-механических свойств материала деталей.
Размеры детали изменяются из-за её износа. Так как на детали при работе двигателя действуют знакопеременные нагрузки, детали изнашиваются неравномерно, и общему износу деталей сопутствует изменение их геометрической формы. Так, вследствие неравномерного давления поршня на цилиндр, цилиндры двигателя в плане изнашиваются «под овал», а в разрезе под бочкообразный конус. В верхней части цилиндра формируется износный уступ, образованный верхним компрессионным кольцом. Овальность цилиндров может быть вызвана, в том числе тепловой или механической деформацией блока цилиндров. Шейки коленчатого вала так же изнашиваются «под овал». Наибольший износ шатунных шеек наблюдается со стороны коренных шеек.
Отклонения в точности взаиморасположения деталей выражаются в нарушениях параллельности и перпендикулярности осей валов и плоскостей корпусных деталей, соосности, межосевого расстояния, в торцевом биении и т.п. Эти отклонения могут быть вызваны недопустимым напряжением в деталях, чрезмерными перегрузками во время работы и др. факторами. У коленчатого вала часто наблюдается биение шеек и фланца маховика, непараллельность шеек, отклонения в радиусах колен. В результате коробления блоков цилиндров двигателя и головки блока цилиндров возникает несоосность постелей коренных опор коленчатого и распределительного валов, не перпендикулярность осей цилиндров двигателя и коленчатого вала, нарушение межосевых расстояний цилиндров и др. Подобные нарушения приводят к появлению дополнительных нагрузок, к повышенному износу деталей и их преждевременному выходу из строя. Вследствие возникающих напряжений металла, повышенных или недопустимых механических и термических нагрузок на детали проявляются «усталостные» трещины, разрывы, изломы, изгибы, скручивания, коробления и т.п.
Коррозия деталей возникает там, где детали соприкасаются с агрессивными и, коррозирующими средами, такими как охлаждающие жидкости, выхлопные и картерные газы, кислоты, щёлочи и др. Коррозию можно видеть на рабочих поверхностях выпускных клапанов, в верхней части цилиндров двигателя, деталях и рубашке системы охлаждения.
Изменение физико-химических свойств материала деталей, чаще всего характеризуется изменением твёрдости и упругости. Как твёрдость, так и упругость материала и рабочих поверхностей снижается из-за перегрева, износа, «усталости».
Технология измерений.
Как уже отмечалось выше, контрольно-сортировочные операции требуют от исполнителя тщательности, внимания, терпения, владения определёнными навыками и умения работать с измерительным инструментом. И, если навык работы с инструментом приобретается непродолжительной практикой, то тщательность и терпение зависит только от Ваших личных качеств.
Проверка состояния деталей двигателя начинается и заканчивается визуальным осмотром. Такие повреждения деталей как: коррозия, трещины, сколы, риски, царапины, борозды, задиры, выкрашивание поверхности и т.п. достаточно легко определить на ощупь и визуально. Обладая определённым опытом и навыками визуально можно оценить и менее видимые для глаза повреждения, такие как несоосность, неплоскостность, нарушение геометрии формы и т.д. И, тем не менее, следует понимать, что гладкая поверхность детали не является гарантированным показателем её (детали) идеального состояния. Обладая ровной (для глаза и на ощупь) рабочей поверхностью, деталь может иметь значительный износ и быть непригодной для повторной установки в двигатель. Такие «неочевидные» и «неуловимые», для визуальной диагностики, количественные оценки повреждения детали как степень износа, величина износа и деформации формы, определяются инструментальными методами с помощью измерительных инструментов.
Деформация валов контролируется на призмах с помощью индикатора часового типа, закреплённого на специальной стойке. Призмы представляют собой «металлические подставки» на которые, своими крайними опорами устанавливается вал, и на которых он легко может вращаться. Сами призмы ставятся на ровную жёсткую поверхность (например, на стальную плиту). Ножку измерительного устройства опирают поочерёдно на одну из средних опор (шеек) вала. Деформация вала определяется по максимальному отклонению от нулевого положения стрелки индикатора при повороте вала в призмах вокруг своей оси. Для большинства современных двигателей величина «биения» средних шеек коленчатого вала относительно крайних шеек не должна превышать 0, 05 мм. Схема, поясняющая сказанное показана на рис. 6.3.
Напоминаю, что все приводимые величины отклонений, номинальных размеров, износов, зазоров, размеров, допусков и посадок и т.п, являются ориентировочными. При ремонте конкретного двигателя следует полагаться на данные изготовителя и данные, указанные в сервисной литературе по ремонту ВАШЕГО двигателя.
При отсутствии у Вас необходимого оборудования для проведения самостоятельной проверки, можно попросить проконтролировать биение вала в станочной мастерской, куда Вы отвозите валы на шлифовку. Вал закрепляется на токарном станке по, имеющимся на нём, установочным базам.
Следует различать основные и вспомогательные установочные базы. Основными базами являются поверхности, используемые как для закрепления детали на станке, так и для соединения её с другой деталью узла или агрегата. Например, посадочные отверстия шестерён, шейки валов, пояса гильз, являются основными установочными базами. Вспомогательные установочные базы создаются только для точной установки обрабатываемой детали на станок.
Размеры шеек коленчатого вала удобно измерять микрометром. С целью определения неравномерности износа (овальности) шатунных шеек, измерение шеек производят в двух направлениях: по радиусу кривошипа и перпендикулярно к нему (рис. 6.4). Допустимая овальность шеек не должна быть больше 0, 010 – 0, 015 мм.

Предельный износ шейки вала не должен быть больше предельно-допустимого размера, установленного изготовителем. Величина износа кулачков распределительного вала определяется измерением их высоты.
Коренные и шатунные вкладыши коленчатого вала при ремонте двигателя лучше заменять новыми. Если предполагается оставить старые вкладыши, будет не лишним проконтролировать их толщину, износ и распрямление. Под распрямлением следует понимать разницу между наружным диаметром вкладыша в свободном состоянии и диаметром постели (рис. 6.5). Если распрямление вкладыша меньше 0, 5 мм, то его лучше заменить, так как малое распрямление не обеспечит необходимый натяг вкладыша в постели.
Измерение диаметров постелей валов, отверстий нижних головок шатунов, цилиндров и иных отверстий осуществляется нутромером. Перед выполнением измерения нутромер устанавливается «на ноль» с помощью кольцевого калибра или микрометра (рис. 6.6а).
Общий износ деталей двигателя, часто рекомендуется определять по величине зазора между парами трения. Номинальная и предельная величина этого зазора регламентируется техническими условиями. Например, зазор в паре трения цилиндр – поршень у современных двигателей может быть меньше 0, 04 мм, а его предельная величина, для разных моделей двигателей, не должна превышать 0, 10 – 0, 20 мм. Истинная величина зазора между этими деталями определяется как разница замеренных диаметров цилиндра и поршня этого цилиндра. Так как цилиндр изнашивается неравномерно, то диаметр цилиндра измеряют на нескольких уровнях (поясах) в двух взаимно перпендикулярных осях. На рис. 6.6б показана возможная (рекомендуемая для определённой модели двигателя) схема замера цилиндра. В силу конструктивных особенностей поршня измерение диаметра поршня производится в строго определённом месте. Как правило, в плоскости перпендикулярной оси поршневого пальца, лежащей немногим ниже отверстия под поршневой палец. Расстояние от днища поршня до плоскости, в которой измеряется диаметр поршня, приводится в технической литературе по ремонту.
Если износ цилиндров превышает предельную величину, цилиндры подлежат растачиванию под ремонтные размеры, а гильзы замене. Для многих современных двигателей предельным считается износ, превышающий 0, 12 мм. При износе цилиндра меньше 0, 10 мм и при удовлетворительном состоянии зеркала цилиндра, в двигатель устанавливаются поршни и кольца номинального размера, цилиндры при этом не растачиваются. При проведении измерений и установлении величины износа следует помнить, что цилиндры двигателя по номинальному размеру делятся на категории (группы, классы). Например, цилиндры отечественного автомобиля ВАЗ, делятся на пять основных категорий, которые обозначаются латинскими буквами A, B, C, D, E. Диаметр цилиндра каждой последующей категории отличается от предыдущей на +0, 01 мм. То есть, при номинальном диаметре цилиндра равным, например, 79, 00 мм, диаметр цилиндра категории «Е» будет отличаться от диаметра цилиндра категории «А» на 0, 040 – 0.050 мм. ( A 79.000 – 79.010, B 79.010 – 79.020, C 79.020 – 79.030, D 79.030 – 79.040, E 79.040 – 79.050). Во избежание ошибки при вычислениях, износ цилиндра целесообразно рассчитывать с учётом его категории.
Возможные места маркировки размерной группы цилиндров на блоке, показаны на рис. 6.7.
Износ опор и подшипников (постелей) распределительного вала определяется как разница между измеренными значениями диаметра отверстия постели и опоры (шейки) вала. Вычисленный зазор не должен превышать 0, 10 мм. Зазор в паре трения вал – опора может быть вычислен и с помощью мерной проволоки. Проволока подкладывается под вал в опору, крышки вала затягиваются номинальными усилиями. После разборки соединения толщину проволоки (величину сплющивания) измеряют микрометром или с помощью специальной шкалы. Измеренная толщина и есть зазор в паре трения. Измерение ширины калиброванной проволоки после сплющивания с помощью шкалы показано на рис. 6.8
Диаметры отверстий опор коленчатого вала и отверстий в нижних головках шатунов измеряются при затянутых крышках. Усилия затяжки крепежа должны соответствовать рекомендованным заводом изготовителем. Схема проверки внутреннего диаметра опоры
коленчатого вала в сборе с подшипником, показана на рис. 6.9.
Для контроля соосности опор вала можно воспользоваться лекальной линейкой (плоскопараллельным бруском). Линейка устанавливается на три близлежащие опоры по оси этих опор. Несоосность или деформация опор обнаруживается по «покачиванию» линейки на центральной, из трёх выбранных опор. Величина несоосности измеряется щупами, подкладываемыми под линейку.
Износ рабочей (наружной) поверхности колец определяется визуально (на изношенных кольцах сточены маслосъёмные гребни) или по величине замка. Для современных двигателей предельная ширина замка колец установленных в цилиндр (в его неизношенную часть) не должна превышать 0, 7 – 2, 0 мм. Толщину (высоту) кольца удобнее измерить микрометром.
При проведении дефектации деталей двигателя в обязательном порядке проверяется деформация плоскостей блока цилиндров и головки блока цилиндров. Измерения выполняются с помощью лекальной линейки и набора щупов. Линейка укладывается на плоскость по диагонали. В зазор (если он имеется) между плоскостью детали и плоскостью линейки вводится щуп. Если величина неплоскостности превышает предельную, установленную для данной детали, плоскость восстанавливают. Предельная величина неплоскостности привалочной поверхности головок блока цилиндров, для различных двигателей современной конструкции, лежит в пределах 0, 05 – 0, 10 мм.
Причинами деформации плоскостей корпусных деталей двигателя может быть перегрев двигателя (часто многократный) и чрезмерная затяжка гаек (болтов) крепления головки блока цилиндров. Перегрев двигателя приводит к «проседанию» (провалу) средней части плоскости, а «перетяжка» крепежа к появлению выпучиваний у отверстий болтов и деформации цилиндров.
Методы и способы измерения других деталей, аналогичны методам, описанным выше.
Серьёзной проблемой в диагностике является обнаружение трещин. Наличие необнаруженных трещин в корпусных или иных деталях двигателя, может свести к нулю все усилия, затраченные на ремонт. Можно выделить несколько методов выявления трещин, применяемых сегодня на ремонтных предприятиях, имеющих различную степень оснащённости.
- Метод гидравлической опрессовки;
Заключается в подаче под давлением 6 – 8 атм. жидкости во внутренние полости детали. При этом все отверстия, имеющие выход наружу, должны быть герметично закрыты. При наличии трещин в детали, через них будет вытекать (просачиваться) закачиваемая в полости жидкость. - Метод пневматической опрессовки;
Метод аналогичен методу, описанному выше. В полости детали, погруженной в горячую воду, подаётся сжатый воздух. Наличие трещин фиксируется по истечению пузырьков воздуха.
Метод гидравлической и пневматической опрессовки широко практикуется для диагностики корпусных деталей двигателя. - Метод цветной дефектоскопии;
Суть метода заключается в том, что на деталь наносят специальный проникающий раствор, окрашенный в красный (или иной) цвет. Раствор, в силу высокой проникающей способности, способен затекать глубоко в трещины шириной в тысячные доли мм. После мойки поверхности детали, на деталь наносят проявляющий раствор белого цвета. Имеющиеся трещины проявляются розовым цветом на белом фоне. - Метод магнитной дефектоскопии;
Данный метод используется при диагностировании деталей из чугуна или стали. Деталь намагничивают, помещая её в поле электромагнитов. При наличии в детали трещин, магнитное поле в зоне трещины искажается. При нанесении на деталь ферромагнитного порошка или суспензии, трещина проявляется скоплением вдоль неё магнитного материала. - Метод ультразвуковой дефектоскопии;
Ультразвуковая дефектоскопия основана на принципе отражения ультразвуковых импульсов определённой частоты от детали. Дефекты детали диагностируются по искажению отражённой волны на экране дефектоскопа. - Метод рентгенодефектоскопии.
Метод основан на просвечивании детали рентгеновским излучением.
6.7. Ремонт деталей.
Детали двигателя имеют различную, часто сложную форму и конфигурацию, они изготовлены из различных материалов с применением различных технологий, а также могут иметь соответствующим способом обработанные рабочие поверхности, в связи с чем, способы и методы ремонта этих деталей различаются. Тем не менее, обобщённо, весь ремонт двигателя сводится к 1) ремонту отверстий, 2) ремонту валов и 3) ремонту корпусных деталей.
6.7.1. Ремонт отверстий.
Ремонт отверстий в деталях двигателя выполняется одним из двух способов. Изношенные отверстия либо растачиваются под ремонтные размеры, либо восстанавливаются до номинального размера. Растачиванию под ремонтные размеры подвергаются цилиндры и гильзы цилиндров. Восстановлению подлежат постели шеек коленчатого и распределительного валов, отверстия головок шатунов и т.п. Для расточки отверстий используются расточные и токарные станки. Для восстановления изначальных размеров детали используют методы наплавки, наварки и порошкового напыления. При любом из перечисленных способов, рабочие поверхности отверстия, подвергаются окончательной (финишной) обработке на специальном оборудовании. Для окончательной обработки широко применяются хонингование, выполняемое на специальных хонинговальных станках. Рабочим инструментом хонинговального станка является хонинговальная головка – хона с абразивными брусками. Хонинговальная головка, закреплённая на хонинговальном или вертикально-сверлильном станке, одновременно совершает возвратно-поступательные и вращательные движения. Бруски прижимаются к обрабатываемой поверхности механически (например, пружинами), от руки, сжатым воздухом или иначе.
Для обработки алюминиевых, бронзовых и чугунных деталей используются бруски из окиси алюминия Al2O3 или карбида кремния SiC. Для обработки стальных деталей могут использоваться алмазные бруски или бруски из нитрата бора.
Задача хонингования – получение качественной рабочей поверхности, гладкой и одновременно в меру шероховатой, способной удерживать масло для смазки ответной детали, например, поршня. Создание такой поверхности достигается применением качественного абразивного материала и специальными способами и методами (технологиями) хонингования. На рис. 6.10 показан участок поверхности цилиндра после хонингования.
Обработка отверстия под ремонтные размеры является наиболее распространённым и дешёвым способом восстановления деталей. Следует различать обработку деталей (отверстий деталей) под стандартные и свободные ремонтные размеры. Стандартные ремонтные размеры определены техническими условиями на ремонт и, в связи с тем, что увеличение диаметра отверстия детали предполагает использование ответной детали увеличенного (ремонтного) размера, именно в этих размерах промышленно изготавливаются запасные части автомобилей. Для чугунных блоков цилиндров стандартный «ремонтный шаг» (ряд) может составлять +0, 2 мм; +0, 4мм…, или +0, 3 мм; +0, 6 мм…, а также +0, 25 мм; +0, 50 мм, и т.д. Цилиндры цельноалюминиевых блоков без покрытия ремонтируются аналогичным образом, а после расточки протравливаются кислотой с целью проявления на рабочей поверхности цилиндров молекул кремния. Молекулы кремния образуют на поверхности цилиндра слой, способный противостоять износу длительный период эксплуатации двигателя. Цилиндры с покрытием рабочей поверхности типа «Никасил» имеют несколько иную технологию ремонта, которая не предусматривает расточку на большую глубину. Впрочем, как правило, этого и не требуется из-за незначительных износов таких цилиндров, даже при существенных пробегах автомобиля. Следует понимать, что все цилиндры двигателя должны растачиваться под один и тот же ремонтный размер. При расточке цилиндра оставляется припуск на каждую сторону цилиндра не менее 0, 05 мм. под последующее хонингование. Целью ремонта отверстий деталей в целом и цилиндров в частности является:
- Восстановление поверхности цилиндров (отверстий);
- Восстановление геометрии отверстий;
- Восстановление величины зазора между цилиндром и охватываемой деталью;
- Восстановление взаимного расположения деталей.
6.7.2. Ремонт валов.
Основными неисправностями валов двигателей являются: 1) естественный износ шеек и кулачков, вследствие длительной эксплуатации; 2) задиры шеек и кулачков, вследствие масляного голодания или попадания в пару трения опора – шейка посторонних частиц, а также 3) деформация валов, вследствие воздействия на них предельных нагрузок. Валы должны быть тщательно вымыты, осмотрены и измерены. При естественном износе шеек вала, рабочие поверхности часто остаются гладкими без видимых повреждений, а величины износов относительно невелики и обычно не превышают 0, 08 мм, при овальности шеек 0, 02 – 0, 03 мм. Повреждение шеек в результате разрушения подшипников опор более значительные. Износ шеек, в подобных случаях может достигать десятых долей мм.
Любой износ шеек валов и их опор (подшипников), приводит к увеличению зазора между ними, как следствие, ухудшению смазки (падает давление масла, исчезает «масляный клин» между деталями), что, в свою очередь, провоцирует прогрессирующий износ, приводящий к разрушению деталей, проворачиванию вкладышей или заклиниванию вала в опорах.
Изношенные валы подвергаются шлифовке шеек под ремонтные размеры, наплавке шеек и кулачков с их последующей обработкой под номинальные размеры и правкой имеющихся деформаций с последующей балансировкой вала. Целью проводимого ремонта является:
- Восстановление зазоров в сопряжении деталей до номинальных значений;
- Восстановление геометрии шеек;
- Восстановление поверхности деталей;
- Восстановление взаимного расположения поверхностей вала и его опор (соосности, перпендикулярности и т.п.).
«Ремонтный шаг» шеек коленчатого вала, как правило, равен 0, 25мм. Вал может иметь два, три, четыре и более ремонтов. Число ремонтов вала, как правило, регламентируется изготовителем и во многом зависит от размерности, выпускаемых заводами ремонтных деталей (в частности, вкладышей коленчатого вала) и их наличия. При отсутствии «заводских» вкладышей и наличия соответствующего оборудования, вкладыши можно изготовить самостоятельно. В этом случае глубина шлифовки соответствующей шейки (т.е. номер ремонта), будет определяться глубиной её закалки. Глубина закалки коленчатых валов двигателей легковых автомобилей, как правило, немногим более 1мм. Одноимённые шейки коленчатого (распределительного) вала шлифуются под одинаковый ремонтный размер.
Как мы уже знаем, целью шлифовки является восстановление геометрии и поверхности шеек вала. Так как при шлифовке шеек вала их диаметр уменьшается, для сохранения величины установочного зазора между валом и его опорами в опоры должны устанавливаться вкладыши, соответствующей ремонтной группы (т.е. имеющие толщину большую толщины вкладыша номинального размера на величину выполненного ремонта). Ремонтный размер вкладышей, как правило, выбивается в виде цифры (+0, 25; +0, 50; +0, 75 и т.п.) на его тыльной (не рабочей) поверхности.
Обкатка двигателя.
Начальную обкатку отремонтированного двигателя необходимо производить перед сдачей автомобиля заказчику с целью приработки деталей друг к другу. Новые и отремонтированные детали могут иметь повышенную шероховатость поверхностей и отклонения формы поверхностей, что приводит к уменьшению площади контакта прирабатываемых «пар трения» и увеличению на поверхности удельных нагрузок (рис. 6.30).

Увеличение нагрузок на детали, в свою очередь, приводит к их повышенному износу, образованию большого количества продуктов износа, и к поломкам.
Следует различать два типа начальной обкатки двигателя: 1) холодная обкатка и 2) горячая обкатка.
Холодная обкатка двигателя производится на стенде. Стенд имеет в своём составе электродвигатель, обороты которого регулируются, например, с помощью реостата. Электродвигатель соединяется с маховиком коленчатого вала обкатываемого двигателя. Период холодной обкатки длится 15 – 20 минут. Обороты электродвигателя (коленчатого вала) повышаются постепенно и не должны превышать 2500 оборотов в минуту. Двигатель должен быть заправлен моторным маслом, давление в системе смазки контролируется по манометру, вкрученному в масленую магистраль.
Горячая обкатка проводится на полностью собранном двигателе, заправленным маслом и охлаждающей жидкостью. Двигатель запускается и прогревается до рабочей температуры. На тех двигателях, где это необходимо производится регулировка оборотов холостого хода и зажигания. В процессе работы двигателя контролируется давление масла и температурный режим, двигатель осматривается на наличие подтекания масла и охлаждающей жидкости, производится прослушивание двигателя на обнаружение посторонних шумов и стуков. Продолжительность горячей обкатки от 30 минут до 1, 5 часов и более. При проведении обкатки следует соблюдать некоторые правила: 1) обороты КВ не должны быть ниже 1100 оборотов в минуту (на оборотах холостого хода смесь несколько переобогащена, что не очень хорошо сказывается на работе двигателя), при этом увеличивать обороты следует исключительно за счёт увеличения подачи в цилиндры топливно-воздушной смеси (но не её обогащением); 2) не следует поднимать обороты КВ больше 3000 оборотов в минуту, работа двигателя на оборотах больше 2500 оборотов в минуту допускается непродолжительное время; 3) увеличивать обороты КВ следует постепенно.
Передача отремонтированного автомобиля заказчику. Если в процессе предварительной обкатки все системы и механизмы двигателя функционируют нормально, вымытая машина с чистым салоном передаётся заказчику. Дальнейшая, эксплутационная обкатка двигателя осуществляется владельцем автомобиля в течение первых 1, 5 – 2 тысяч км пробега.
6.12. Гарантийное обслуживание.
Гарантийное обслуживание отремонтированного автомобиля осуществляется техническим центром, проводившим ремонт. Гарантийный срок также устанавливается СТО, с учётом сложившейся практики для конкретной модели автомобиля и его года выпуска. Как правило, это один год эксплуатации или 10000 км пробега, что раньше наступит. Первые 1, 5 – 2, 0 тысячи км эксплуатации отремонтированного двигателя являются наиболее ответственным периодом – периодом обкатки. В этот период владельцу автомобиля следует придерживаться некоторых не очень обременительных, но очень важных правил, которые позволят избежать появления неисправностей, связанных с ошибками в эксплуатации.
- Перед началом движения двигатель должен прогреваться до рабочей температуры;
- Следует избегать перегрузки двигателя по оборотам и крутящему моменту. Максимальные обороты коленчатого вала следует ограничить значением 4000 оборотов в минуту для бензинового и 3000 оборотов, для дизельного двигателя. Минимальные обороты на третьей и более высоких передачах не должны быть меньше 2000 и 1500 оборотов в минуту для бензинового и дизельного двигателя соответственно. Каждому режиму движения следует строго выбирать соответствующую передачу в коробке передач;
- В период обкатки следует применять более жидкое масло, чем в последующий период эксплуатации;
- Перегрев двигателя, работа двигателя с пониженным давлением масла и на богатых топливных смесях недопустима;
После периода обкатки автомобиль должен пройти техническое обслуживание на СТО. При техническом обслуживании производится замена моторного масла и масленого фильтра, а также проводится весь объём работ ТО №2
Кузов
Кузовы легковых автомобилей, по большей части имеют несущую конструкцию, которая предполагает крепление основных узлов и агрегатов непосредственно к его корпусу. Немногим реже встречаются легковые автомобили, имеющие кузов с несущим основанием или подрамником, ещё реже - рамную конструкцию. Несущий кузов получил распространение с 50-х годов прошлого столетия.
Корпус несущего кузова рис. 1.2 объемный, из листового металла толщиной 0, 5 –2, 0 мм, представляет собой жесткую сварную конструкцию, состоящую из отдельных, предварительно собранных узлов: 1)основания (пола) с передней и задней частями корпуса; 2) левой и правой боковин со стойками дверей и задними крыльями; 3) крыши и 4) передних крыльев. Жёсткость кузова обеспечивается наличием в его составе большого числа профильных элементов из штампованных деталей, которые при соединении создают закрытые коробчатые сечения.
Тип кузова определяется числом функциональных отсеков (объёмов) и конструктивным исполнением. Изготовителями выпускаются автомобили с трёх, двух, и однообъёмными кузовами.
Трёхобъёмный кузов имеет в своём составе моторный отсек, салон и багажное отделение (например, лимузин, купе, седан, кабриолет, хардтоп).
Двухобъёмный кузов имеет моторный отсек и салон, совмещённый с багажным отделением, расположенным в задней части салона (например, универсал, комби, фастбек, хэтчбек).
В однообъёмном кузове моторный отсек, салон и багажник объединены в одно целое (например, минивэны с центральным расположением силового агрегата, пассажирские фургоны типа «буханка»).
Кузов может быть открытым или закрытым. Открытый тип кузова имеет съёмную крышу или складывающийся верх, выполненный из матерчатого или пластикового тента (например, кабриолет, родстер, фаэтон, ландо).
Грузовые типы кузовов легковых автомобилей также могут быть открытыми – «пикап», или закрытыми – «фургон». Грузовая часть кузова таких автомобилей отделена от водителя и пассажиров стационарной перегородкой.
Некоторые типы кузовов легковых автомобилей представлены на рис. 1.3
Шасси
Шасси автомобиля обеспечивает передачу усилия от двигателя к ведущим колёсам, управление автомобилем и его передвижение. В состав шасси входит: 1) силовая передача (трансмиссия); 2) ходовая часть и 3) механизмы управления.
Трансмиссия
Трансмиссия осуществляет передачу крутящего момента от коленчатого вала двигателя к ведущим колёсам, трансформируя его (крутящий момент) в зависимости от условий движения автомобиля. Силовые передачи автомобилей могут иметь существенные отличия.
По степени приспособленности к различным дорожным условиям и назначению, силовые передачи можно разделить на: 1) трансмиссию автомобилей классической компоновки; 2) трансмиссию автомобилей с приводом на передние колёса; 3) трансмиссию автомобилей повышенной проходимости с «колёсной формулой – 4х4»; 4) трансмиссию автомобилей дорожной проходимости с «колёсной формулой – 4х4».
Расположение узлов и агрегатов трансмиссии автомобилей различного назначения показаны на рис. 1.4.
Автомобиль классической компоновки имеет привод на задние колёса и переднее продольное размещение силового агрегата. Трансмиссия такого автомобиля состоит из: 1) сцепления, 2) коробки передач, 3) карданной передачи и 4) ведущего моста, в котором размещается главная передача с дифференциалом и полуосями.
Сцепление обеспечивает соединение двигателя и трансмиссии при движении автомобиля, а также осуществляет передачу вращения от коленчатого вала на валы коробки передач. Когда при изменении условий движения необходимо переключить передачу сцепление отсоединяет вал двигателя от трансмиссии. Сцепление легковых автомобилей, имеющих механическую трансмиссию - фрикционное, сухое с одним ведомым диском и механическим или гидравлическим приводом.
Однодисковое фрикционное сцепление имеет 1) ведомый диск со ступицей, гасителем крутильных колебаний ( демпфером ) и фрикционными накладками; 2) нажимной диск; 3) диафрагменную нажимную пружину; 4) кожух сцепления и некоторые другие детали.
Общее устройство сцепления легкового автомобиля показано на рис. 1.5
В автомобилях с автоматическими трансмиссиями используются гидродинамические трансформаторы и коробки передач, действующие автоматически, в зависимости от скоростного и нагрузочного режима движения автомобиля.
Коробка передач служит для изменения тягового усилия на колёсах, а также для получения заднего хода и отсоединения ведущих колёс от двигателя. На легковых автомобилях, как правило, применяются двух или трёхвальные коробки передач.
В трансмиссиях с ручным или полуавтоматическим переключением передач применяются механические коробки в основном с цилиндрическими шестернями внешнего зацепления.
В автомобилях с автоматическими трансмиссиями применяются как вальные, так и планетарные коробки передач, управление переключением передач в которых осуществляется автоматически многодисковыми сцеплениями, работающими в масляной ванне, и ленточными тормозами, позволяющими переключать передачи без разрыва потока мощности (т.е. без переключения на «нейтральную» передачу). Количество многодисковых сцеплений и ленточных тормозов зависит от числа передач в коробке.
Трансформация передаваемого от двигателя крутящего момента посредством переключения передач в коробке передач достигается введением в зацепление шестерён различного диаметра, меняющих как соотношение между числами оборотов коленчатого вала двигателя и ведущих колёс автомобиля, так и величину тяговых усилий.
Величина изменений указанных характеристик определяется передаточным числом передачи (чем больше передаточное число передачи, тем сильнее изменяется крутящий момент). Передаточное число в общем случае равно отношению числа зубьев (диаметра) ведомой шестерни к числу зубьев (диаметру) ведущей.
Механическая коробка передач имеет корпус, в котором размещаются: 1) первичный, вторичный и промежуточный валы; 2) шестерни передач; 3) синхронизаторы; 4) штоки и вилки переключающего механизма; 5) рычаг переключения передач и другие детали. Общее устройство пятиступенчатой коробки передач показано на рис. 1.6.
Карданная передача осуществляет передачу усилия от коробки передач на главную передачу ведущего моста автомобиля. Вследствие того, что при движении автомобиля его ведущий мост совершает колебания в вертикальной и горизонтальной плоскостях, карданная передача должна передавать крутящие моменты при постоянно изменяющихся углах наклона между валами и расстояниях между передней и задней осями.
Карданная передача состоит из: 1) карданного вала (валов); 2) карданных шарниров или шарниров равных угловых скоростей; 3) промежуточных опор и эластичных муфт карданного вала (валов). Устройство карданной передачи полноприводного автомобиля показано на рис. 1.7.
Главная передача обеспечивает передачу крутящего момента с карданного вала на полуоси под углом 90° и изменяет крутящий момент в соответствии со своим передаточным числом. Главные передачи легковых автомобилей по большей части одинарные и состоят из двух шестерён – ведущей и ведомой. Ведущая шестерня приводится в движение от карданного вала. Ведомая шестерня крепится к корпусу дифференциала и передаёт вращение на полуоси.
Дифференциал служит для распределения крутящего момента между ведущими колёсами и позволяет им вращаться с разной скоростью при движении автомобиля в повороте или по неровной дороге. Наибольшее распространение имеют дифференциалы с коническими шестернями. Дифференциал состоит из корпуса (коробки) дифференциала, в котором размещаются: 1) полуосевые шестерни; 2) саттелитовые шестерни и 3) ось саттелитов.
Полуоси передают крутящий момент от дифференциала на ведущие колёса автомобиля.
Главная передача с дифференциалом и полуосями устанавливается в балке ведущего моста. Балка моста имеет центральную часть – картер и полуосевые рукава. Балка является задней осью автомобиля и крепится к кузову через элементы подвески. Балки бывают разъёмные и неразъёмные. Устройство ведущего моста с главной передачей и дифференциалом показано на рис. 1.8
Трансмиссия автомобилей с приводом на передние колёса отличается от рассмотренной выше тем, что не имеет заднего ведущего моста и карданной передачи. Главная передача и дифференциал размещаются в дополнительном картере коробки передач, а передача усилий от дифференциала на колёса осуществляется через валы привода передних колёс с шарнирами равных угловых скоростей (ШРУС).
Трансмиссия автомобилей повышенной проходимости «внедорожников» с «колёсной формулой – 4х4» дополнительно имеет вторую коробку передач – раздаточную коробку; несколько карданных передач; два ведущих моста – передний и задний, с главными передачами и межколёсными дифференциалами. Раздаточная коробка, как правило, снабжена понижающей передачей и может иметь межосевой дифференциал (для версий с постоянным (т.е. не отключаемым) приводом на все колёса). Также предусматривается механизм блокировки одного или нескольких дифференциалов. На части техники применяются самоблокирующиеся дифференциалы или дифференциалы повышенного трения, а также механизмы отбора мощности на привод вспомогательных механизмов, например лебёдки.
К внедорожникам предъявляются повышенные требования, касающиеся силы тяги, прочности подвески, кузова, а также других узлов и систем. К компоновочным особенностям таких машин, можно отнести короткую базу и высокий клиренс (дорожный просвет) которые, наряду с вышеперечисленными характеристиками, позволяют преодолевать различную степень бездорожья.
Трансмиссия автомобилей дорожной проходимости с «колёсной формулой – 4х4» предназначена для эксплуатации на дорогах с твёрдым покрытием, но может иметь «компромиссную» конструкцию, т.е. одновременно отвечать требованиям как «внедорожника», так и «обычного» автомобиля с приводом на передние или задние колёса. Чаще всего применяется схема, где передние колёса являются основными ведущими, а задний мост подключается автоматически и по мере необходимости. В качестве механизма автоматического подключения заднего моста используются многодисковые вязкостные муфты или механизмы повышенного трения, размещаемые в раздаточной коробке. Сама раздаточная коробка, как правило, монтируется в одном корпусе с коробкой передач.
Трансмиссия современных автомобилей может иметь электронные или электронно-гидравлические устройства управления силой тяги ведущих колёс, к которым относят противобуксовочную систему (ASR). Противобуксовочная система предотвращает проворачивание колёс относительно дорожного покрытия, при излишнем крутящем моменте тем самым, обеспечивая плавное трогание автомобиля с места, оптимальную тягу на колёсах и поддержание курсовой устойчивости автомобиля.
Ходовая часть
Ходовая часть автомобиля состоит из: 1) несущего основания; 2) передней и задней осей; 3) подвески и 4) колёс.
Несущим основанием легкового автомобиля является несущий кузов или рама. Так же, несущее основание может быть образовано элементами рамы, соединёнными с профильными элементами панели пола. Полученная таким образом конструкция, представляет собой отдельный узел автомобиля. К несущему основанию (кузову или раме) крепятся все части и механизмы автомобиля. На раму устанавливается и сам кузов (кабина).
Передние и задние оси автомобиля могут быть ведущими и неведущими. Ведущими осями являются балки ведущих мостов (переднего и/или заднего). Неведущая ось грузового автомобиля представляет собой стальную балку при помощи рессор соединяемую с рамой. У легковых автомобилей, имеющих независимую подвеску колёс, понятие неведущей передней и задней оси отсутствует. В передней части несущего кузова автомобиля с задней ведущей осью имеется стальная балка – поперечина, прикрепляемая к кузову жёстко. В задней части несущего кузова автомобиля с приводом на передние колёса также имеется поперечная балка, называемая соединителем рычагов, которая присоединяется к кузову через элементы подвески. К балкам крепятся рычаги подвески и другие детали.
Подвеска гасит колебания кузова, возникающие при движении автомобиля, смягчает и поглощает удары колёс о неровности дороги тем самым, обеспечивая больший комфорт водителю и пассажирам, сохранность грузов и эксплутационную безопасность автомобиля. Подвеска автомобилей бывает зависимой и независимой. Следует различать рессорные, рычажные, пружинные, торсионные, гидропневматические и пневматические подвески, а также подвески смешанного типа. Основные типы подвесок показаны на рис.1.9а и рис.1.9 б


Колёса автомобиля могут быть ведущими, ведомыми и управляемыми. Ведущими колёсами могут являться передние колёса, задние колёса или все колёса автомобиля. Если ведущей является одна пара колёс (независимо – передняя или задняя), то автомобиль имеет колёсную формулу 4х2; если ведущими являются все четыре колеса, то – 4х4.
Управляемые колёса у легкового автомобиля – передние.
Управляемые передние колёса устанавливаются на ось с углом развала в вертикальной плоскости, равным 0 - 3° и схождением 2 – 4 мм. Для стабилизации управляемых колёс в среднем положении ось поворота колеса имеет поперечный и продольный наклоны (рис. 1.10.).
Колесо состоит из металлического обода и диска. У штампованных колёс диск с ободом соединяются посредством сварки. У литых и кованых колёс диск и обод выполнен за одно целое. На обод колеса монтируется шина. Шины бывают двух типов – камерные и бескамерные. По способу укладки несущего корда, различают шины радиальные и диагональные, а по форме и рисунку протектора – зимние, летние и всесезонные. Имеются и другие конструктивные различия шин.
Механизмы управления
К механизмам управления относятся рулевое управление и тормоза.
Рулевое управление обеспечивает изменение направления движения автомобиля путём поворота его управляемых колёс. Рулевое управление состоит из: 1) рулевого колеса с валом, установленным в рулевой колонке; 2) рулевого механизма; 3) рулевого привода и некоторых других деталей.
Рулевой механизм обеспечивает передачу усилий от рулевого колеса с валом на детали рулевого привода и далее на рулевую трапецию и управляемые колёса. Большее распространение имеют рулевые механизмы глобоидально-червячного и реечного типа.
К деталям рулевого привода легковых автомобилей с независимой передней подвеской относят рулевую сошку, маятниковый рычаг, среднюю и боковые рулевые тяги, рулевые наконечники, рулевые рычаги поворотных кулаков или стоек и другие детали. В устройстве привода рулевого механизма червячного или реечного типа имеются отличия.
Детали рулевого привода образуют рулевую трапецию. Рулевая трапеция осуществляет одновременный поворот управляемых колёс, при этом, внутреннее к центру поворота колесо должно поворачиваться на больший угол, чем внешнее, для обеспечения качения колёс по окружностям, описанным из одного центра. Следует различать нерасчленённые и расчленённые рулевые трапеции. Нерасчленённую трапецию применяют на автомобилях, у которых управляемые колёса устанавливаются на одной оси, подвешенной через детали подвески к кузову или раме. Расчленённую подвеску используют при независимой подвеске управляемых колёс. Рулевые управления с глобоидально-червячным механизмом и механизмом реечного типа показаны на рис. 1.11
Тормозные системы автомобиля служат для снижения скорости автомобиля и его остановки, а также для удержания автомобиля в неподвижном состоянии. Замедление автомобиля обеспечивает рабочая тормозная система. Удержание автомобиля в неподвижном состоянии на уклоне при остановке или стоянке обеспечивает стояночная тормозная система. Помимо перечисленных систем, которые можно назвать основными, автотранспортные средства оснащаются другими средствами для торможения. На грузовых автомобилях и прицепных устройствах находят применение аварийные, запасные, вспомогательные, а также различные типы моторных тормозных систем. Широкое распространение имеют антиблокировочные системы (ABS).
Управление рабочей тормозной системой осуществляется от ножной педали тормоза. Передача усилий от педали тормоза к рабочим тормозным механизмам реализуется через гидравлический, пневматический и редко механический привод. В автомобилях, оснащённых системами ABS, ASR и системами управления динамикой автомобиля тормозные усилия регулируются ЭБУ (электронными блоками управления). Электронные системы управления тормозами широко используется в электропневматических и электрогидравлических тормозных механизмах.
Основными узлами и деталями рабочей тормозной системы с гидравлическим приводом являются: 1) главный тормозной цилиндр с бачком для тормозной жидкости; 2) рабочие тормозные цилиндры, соединённые с главным тормозным цилиндром и регулятором тормозных усилий трубопроводами; 3) колёсные тормозные механизмы, состоящие из тормозных барабанов или дисков и тормозных колодок; 4) педаль тормоза и усилитель тормозов вакуумного или иного типа.
Стояночный тормоз имеет механический привод и при включении блокирует задние колёса автомобиля. В ряде устаревших конструкций стояночный тормоз воздействует на карданный вал (в настоящее время применение трансмиссионного стояночного тормоза запрещено Правилами ЕЭК ООН и ГОСТ РФ). На грузовых автомобилях с пневмотормозами стояночный тормоз приводится в действие при помощи энергоаккумулятора.
Общее устройство рабочей и стояночной тормозной системы легкового автомобиля показано на рис. 1.12

Глава 2. АВТОМОБИЛЬНЫЕ ДВИГАТЕЛИ.
Двигатель является на автомобиле основным источником механической энергии и используется в качестве силовой установки, приводящей машину в движение. На автотранспортные средства устанавливают двигатели различных конструкций, среди которых большее распространение получили поршневые двигатели внутреннего сгорания (ДВС). Гораздо в меньшей степени используются роторные двигатели внутреннего сгорания (двигатели Ванкеля) , и всё большее число производителей склоняется к применению комбинированных (гибридных) установок , объединяющих в себе поршневой ДВС и электродвигатель. На части техники устанавливаются газотурбинные двигатели и электродвигатели .
Поршневыми двигателями внутреннего сгорания (рис. 2.1) комплектуется большинство современных автомобилей. В поршневых двигателях давление газов, образующееся от сгорания топлива в камере сгорания, воспринимается поршнем, движущимся в цилиндре. Возвратно-поступательное движение поршня посредством кривошипно-шатунного механизма преобразуется во вращательное движение коленчатого вала.
К поршневым ДВС относятся дизельные двигатели, с самовоспламенением топливно-воздушной смеси и двигатели Отто, с воспламенением смеси от постороннего источника тепла, например от электрической искры, образующейся между электродами свечи системы зажигания. Такие двигатели называют двигателями с искровым зажиганием. По конструкции кривошипно-шатунного и газораспределительного механизмов дизельные двигатели и двигатели Отто практически не отличаются.
Роторные двигатели внутреннего сгорания (рис. 2.2) имеют ряд преимуществ перед поршневыми двигателями и ряд недостатков, сдерживающих их широкое применение. С двигателем экспериментировали многие известные автомобилестроительные фирмы, включая Волжский Автомобильный Завод (ВАЗ), но на сегодняшний день, пожалуй, только «Мазда» серийно устанавливает их на
спортивные версии своих машин.
В двигателе Ванкеля роль поршня выполняет ротор, имеющий форму равностороннего треугольника со скруглёнными вершинами и слегка выпуклыми сторонами, вращающийся в овальном корпусе (цилиндре) по сложной траектории (эпитрохоиде).
Комбинированные (гибридные) двигатели имеют в своём составе двигатель внутреннего сгорания и электродвигатель, осуществляющий передачу крутящего момента на коленчатый вал ДВС или непосредственно на ведущие колёса автомобиля. В силу свойства «обратимости электрических машин» электродвигатель, в подобных устройствах, может выполнять функции как стартера, осуществляя вращение коленчатого вала ДВС при запуске и, в определённых условиях, обеспечивая движение автомобиля без его участия, так и генератора, работая на подзарядку аккумуляторных батарей при установившихся режимах движения. Автомобили подобных конструкций отличает высокая топливная экономичность и соответствие современным требованиям экологической безопасности.
Термин «комбинированный двигатель» также применяется для поршневых двигателей, имеющих в своём составе газовую турбину и компрессор (турбокомпрессорный двигатель).
Газотурбинные двигатели, как самостоятельные силовые установки, широкого распространения на автомобильной технике не имеют. Их применение в основном ограничено в качестве вспомогательных агрегатов поршневых двигателей. Например, газотурбинные системы наддува ДВС. Схема турбокомпрессорного двигателя (турбокомпрессора) показана на (рис. 2.3)
Электродвигатели в качестве самостоятельной силовой установки по объективным для сегодняшнего дня причинам на серийных моделях автомобилей практически не используются.